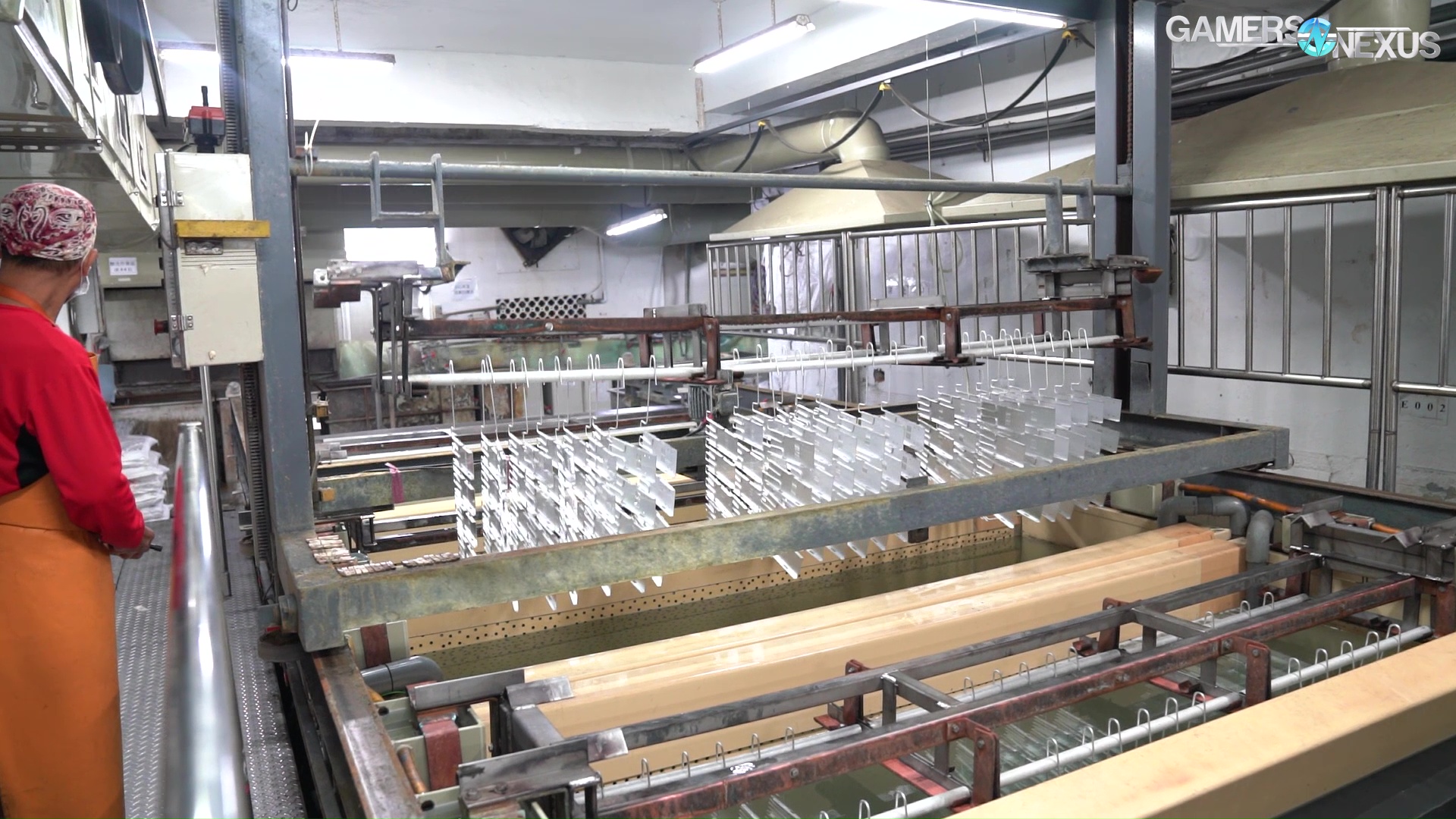
Blasting Electricity at Thousands of PC Parts: How Anodizing Works | Factory Tour
Last Updated:
How component manufacturers coat and color aluminum with tens of thousands of kilowatts of electricity
The Highlights
- Used to create a high quality protective coating on PC components
- The most expensive of the available methods of placing a coating on PC components
- Requires highly caustic chemicals and tens of thousands of kilowatts of electricity
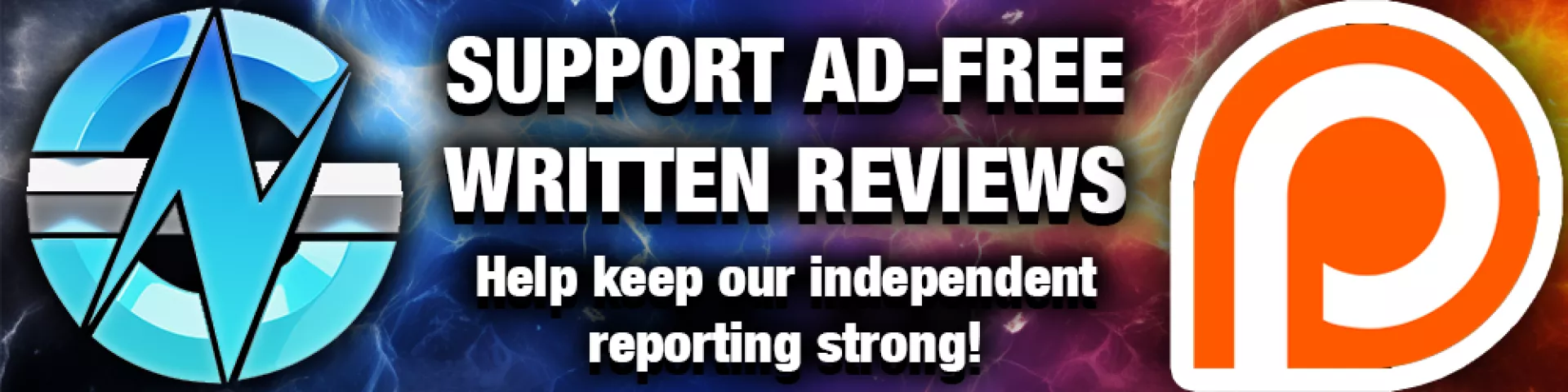
Computer components come in hundreds of different shapes, sizes, and colors. However, some components come out with a more complex coat of paint than others, like the aluminum Yeston CUTE PET case , while others use a simpler paint job. When component manufacturers decide how to coat their products, they typically choose from anodization, painting, electroplating, and electrophoretic deposition, with the cost listed from high-to-low. We’ve observed Noctua coolers getting coated black in our factory visits, using cathodic electrodeposition, and we’ve also seen the robotic arms responsible for painting case side panels like the Lian Li panel made for Digital Storm’s bolt . This article will look specifically at anodization at a third-party factory that Lian Li uses for coating its more expensive components.
The anodization factory we visited is located in northern Taiwan. The factory manager gave us a rundown of the process, from cleaning the parts, stripping them down with chemicals, electrifying them in a bath of acid, coloring them, and finally packing them back up to be returned to the manufacturer.
Editor's Note: This was originally published as a video in April 23 of 2020. This article conversion does not change any of the original editorial content, but is being dated with the article entry date to float it to the top of the website.
Credits
EDITORIAL, REPORTING
Steve Burke
Patrick Latham
video
keegan gallick
Andrew Coleman
WEB Editing
Jack Reitman
How Anodizing Works
Visually, the process of anodizing parts in a factory looks similar to electroplating. Anodizing is fundamentally different in that it doesn’t involve coating one metal in another. Instead, it’s a method of adding an additional oxide layer to the existing metal. Anodization works on many different metals, but is commonly associated with aluminum, which is what this factory specializes in. Aluminum forms an oxide layer on contact with air that naturally protects the metal and prevents further oxidation of the metal underneath, but this natural layer is extremely thin--anodization allows growing a much thicker protective layer that’s easier to dye.
Mounting the Components to Be Anodized
Mounting on aluminum racks Mounting on titanium racks Components to be anodized
The first step of anodization is to fix the aluminum parts onto a conductive metal rack. Two different types of racks are used, depending on the parts that are being coated: titanium racks are stronger and can hold more parts, but the conductivity isn’t optimal, so these are used only for functional parts that are being anodized for protection rather than for aesthetics. Aluminum racks offer better conductivity but hold fewer pieces, and so are used for pieces that are designed to be seen, like Lian Li’s external panels of a case.
Any point where the hooks contact the piece won’t be anodized, so the aluminum hooks are custom-made for each new type of part to minimize contact, while the titanium hooks have a more standardized design. The factory technicians figure out the best spot for each product to attach to the hooks, typically choosing unseen locations like inside of a screw hole. The hooks themselves are anodized during the process, so they won’t last forever, but they are reusable. Factory technicians bring empty titanium racks back from the packing area next door to start the cycle again.
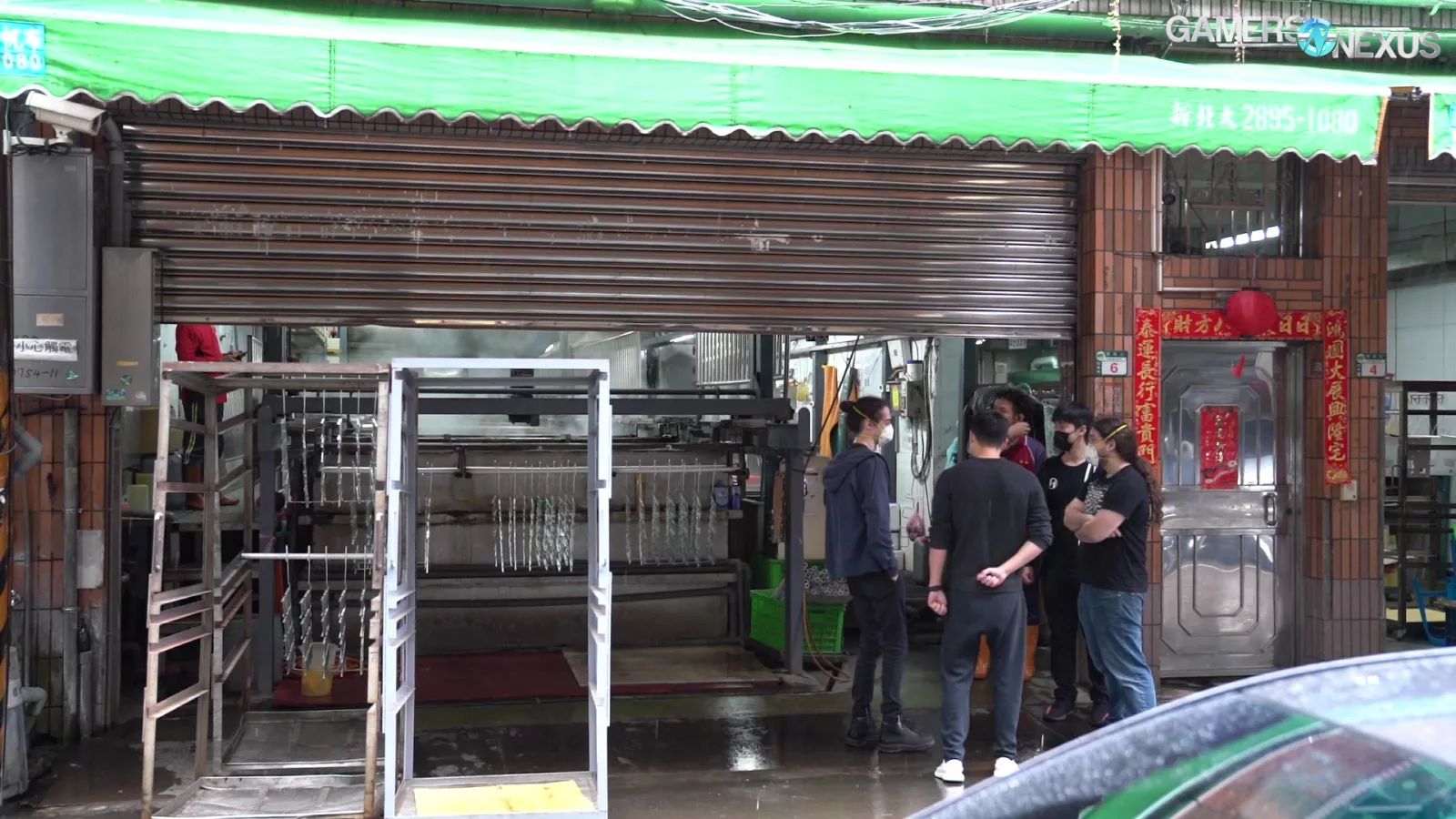
Aluminum comes in many varieties, but the factory most commonly works with 5000 and 6000 series alloys. When asked if some are easier to work with than others, we were told that harder alloys tend to come out grayish, while softer ones produce a better color due to the change in conductivity.
Chemicals and Cleaning
Part cleaning Degreaser vat Running water tank (pictured in back)
Once the parts are secured to a conductive rack, they next have to be cleaned. It’s critical to the operation that the surfaces are clean and free of any fingerprints or other contaminants for the rest of the process, so they’re first cleaned with an oil, and then dunked in a bath of degreaser for 35 minutes, followed by yet another bath of water to rinse off the degreasing fluid and the contaminants that it removed. These tanks are held in the middle of the first room, surrounded by a short concrete curb to hold in splashing and overflow from the water rinse tank, which is being filled with fresh water constantly. The insulated bumpers above these tanks are just to hold the metal poles from which the racks are suspended--electricity isn’t involved until later in the process.
Chemical preparation for the anodization process begins after initial cleaning. The 7 tanks for this stage are lined up against the very back wall of the factory, securely away from the entrance. The first step is pure water cleaning, then the first chemical step is dunking the parts in an alkaline mixture of sodium hydroxide, also known as lye or caustic soda, for about ten seconds. This mixture is kept somewhere between 60 degrees and 70 degrees Celsius and the tanks are visibly steamy, producing a vapor that must be pulled away by a fume hood placed specifically over this end of the line. Lye can cause serious chemical burns, so caution must be exercised here.
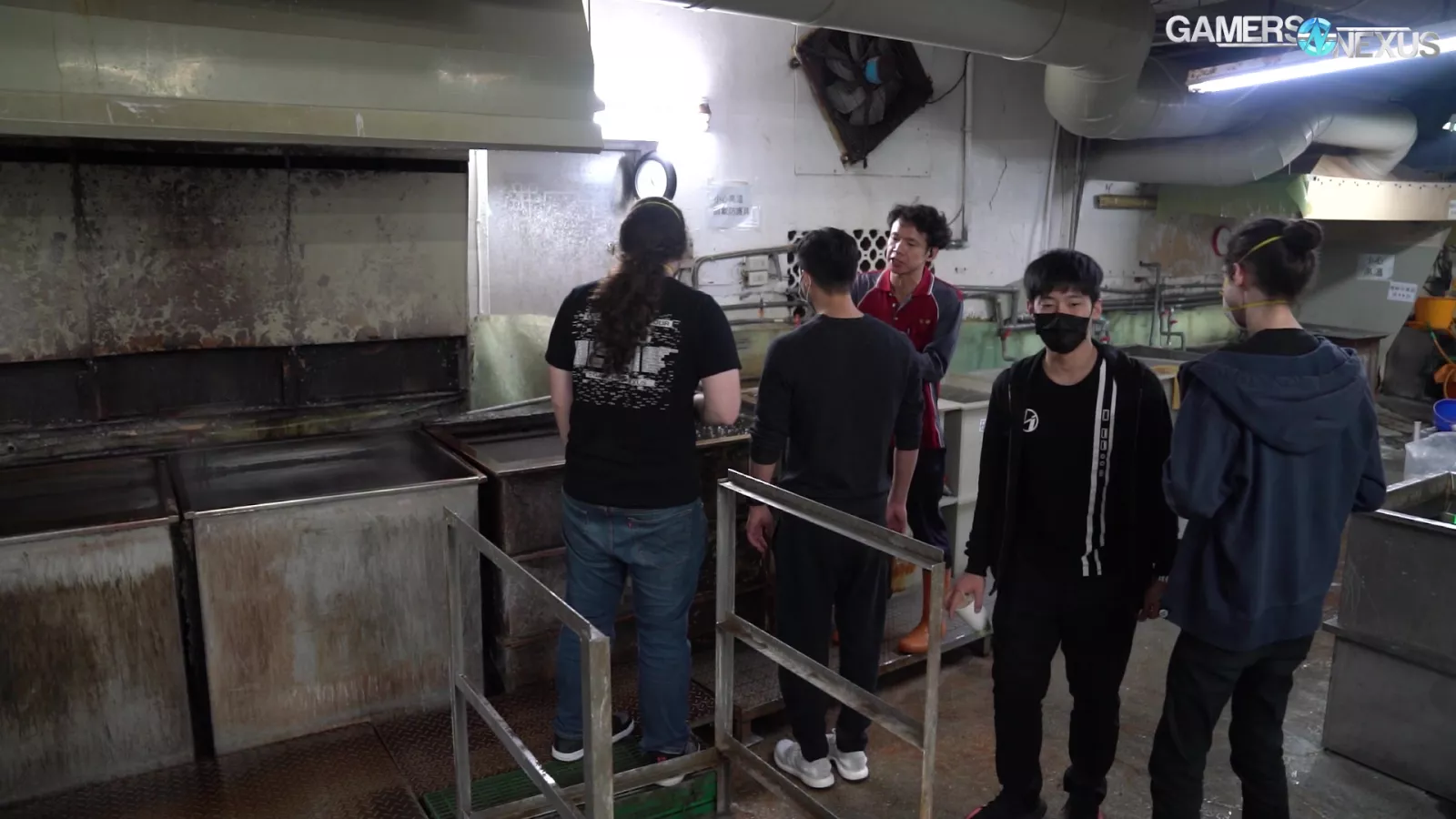
The lye bath is necessary to dissolve the natural layer of aluminum oxide, which lacks the pores required to let oxygen in and grow the oxide layer. Aluminum oxide is amphoteric, meaning it can react with both bases and acids. Sodium hydroxide reacts with it to produce water, aluminate, and heat. Sodium hydroxide also reacts with the raw aluminum underneath to produce aluminate and hydrogen gas, hence limiting the bath to ten seconds. Surface finish is determined at this stage--to make the end result shinier or duller, special chemicals can be used here.
After the ten-second dip, there are five separate water baths, one next to the other, to wash away any remaining traces of sodium hydroxide. Afterwards comes a mixture containing nitric acid. Lye does a great job of eating away aluminum oxide, but aluminum is commonly used as an alloy, and it may not be as effective on the alloyed metals. Diluted nitric acid is used to wash away the residue of other metals in a process known as “desmutting,” followed by yet another series of water baths. Before it’s diluted, the nitric acid is delivered in jugs at 68% concentration--any stronger and it would be considered potentially fuming nitric acid, possibly forming fumes on contact with air, which is undesirable and a safety hazard. The time between putting the parts in the lye bath and finishing the last of the water rinses is approximately ten minutes.
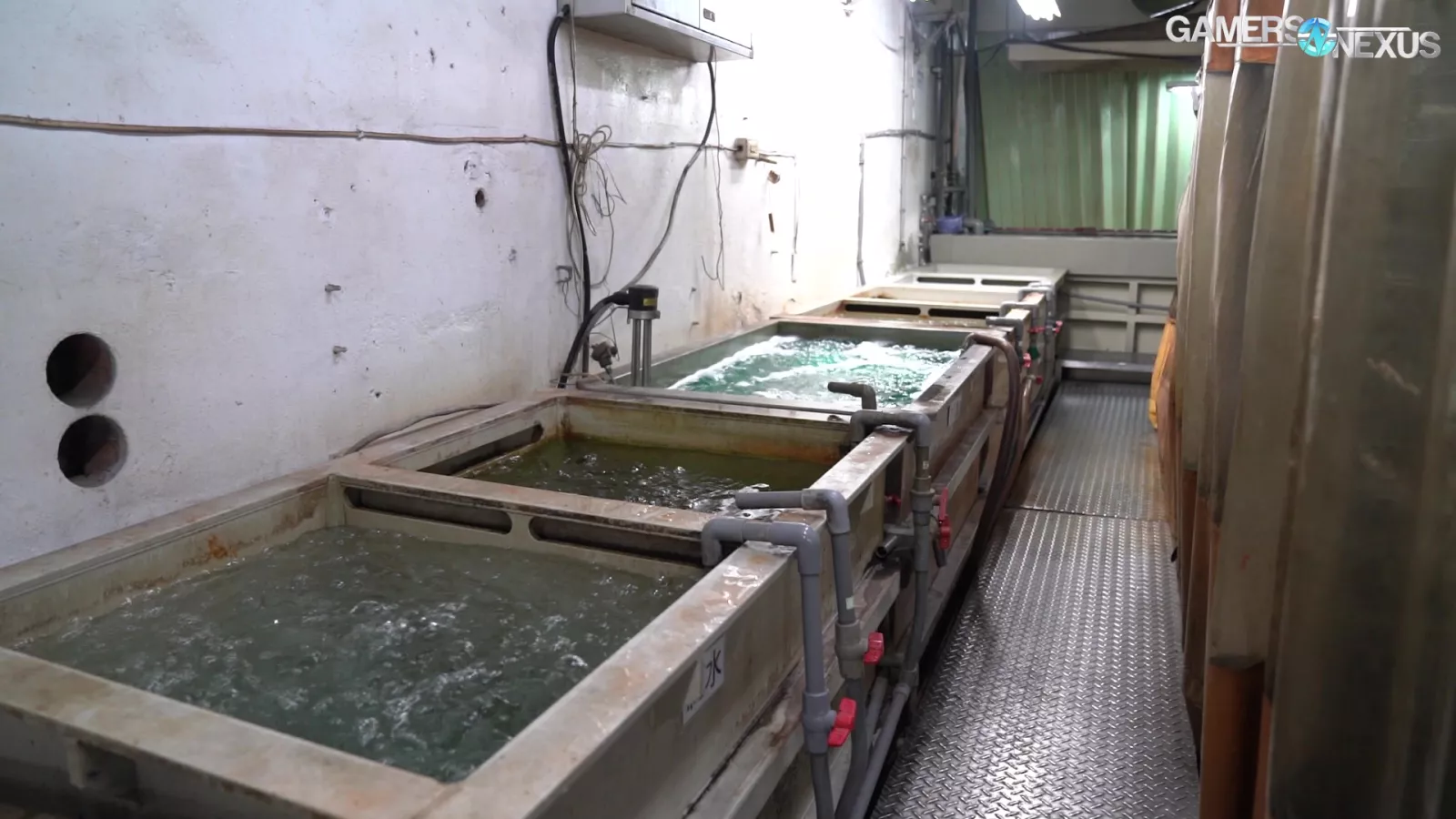
The parts have been completely stripped of any aluminum oxide coating at this point, so it’s vital to prevent contact with the air as much as possible. There are several “standby tanks” of water here for keeping aluminum parts submerged in case the production line gets backed up.
Blasting Electricity at Metal
Anodization line Parts submerged in sulfuric acid solution with electric current passed through Copper anode
Finally, anodization can begin. As with electroplating, the aluminum is submerged in fluid, in this case a solution of 20% sulfuric acid and 80% water held between 20-25C, with an electric current passed through it. The racks containing the aluminum parts are suspended on a metal frame wired up with massive copper strips, through which the current is passed. Wedge-shaped copper slugs at the ends form the contacts. A crane is operated manually at a control station nearby and moves back and forth over the tanks, lifting the frames in and out of the appropriate tanks.
There are only four anodization tanks in this particular line - the rest are for rinsing and coloring. Unlike electroplating, the metal to be anodized is the anode of the circuit, hence the name. The electric current splits water molecules into hydrogen at the cathode and oxygen at the aluminum anode, forming visible bubbles and causing the aluminum to oxidize. The acidic electrolyte bath eats into the oxide layer without completely dissolving it, allowing oxygen to reach even deeper and oxidize even more of the metal, and forms a much thicker and more porous structure than would naturally occur. The end result is an inflexible oxide crust that’s not electrically conductive and is less thermally conductive than the aluminum underneath.
As for power, this line of tanks was running at an impressive 25KW. We were told that the actual anodizing process length is 20-40 minutes, with darker colors taking longer. Black takes about 40 minutes, white or semi-transparent coats take about 20 minutes, and the rest is in between. This process can be started from either side of the line, depending on logistics each day. Parts are rinsed 6 times in water and then colored.
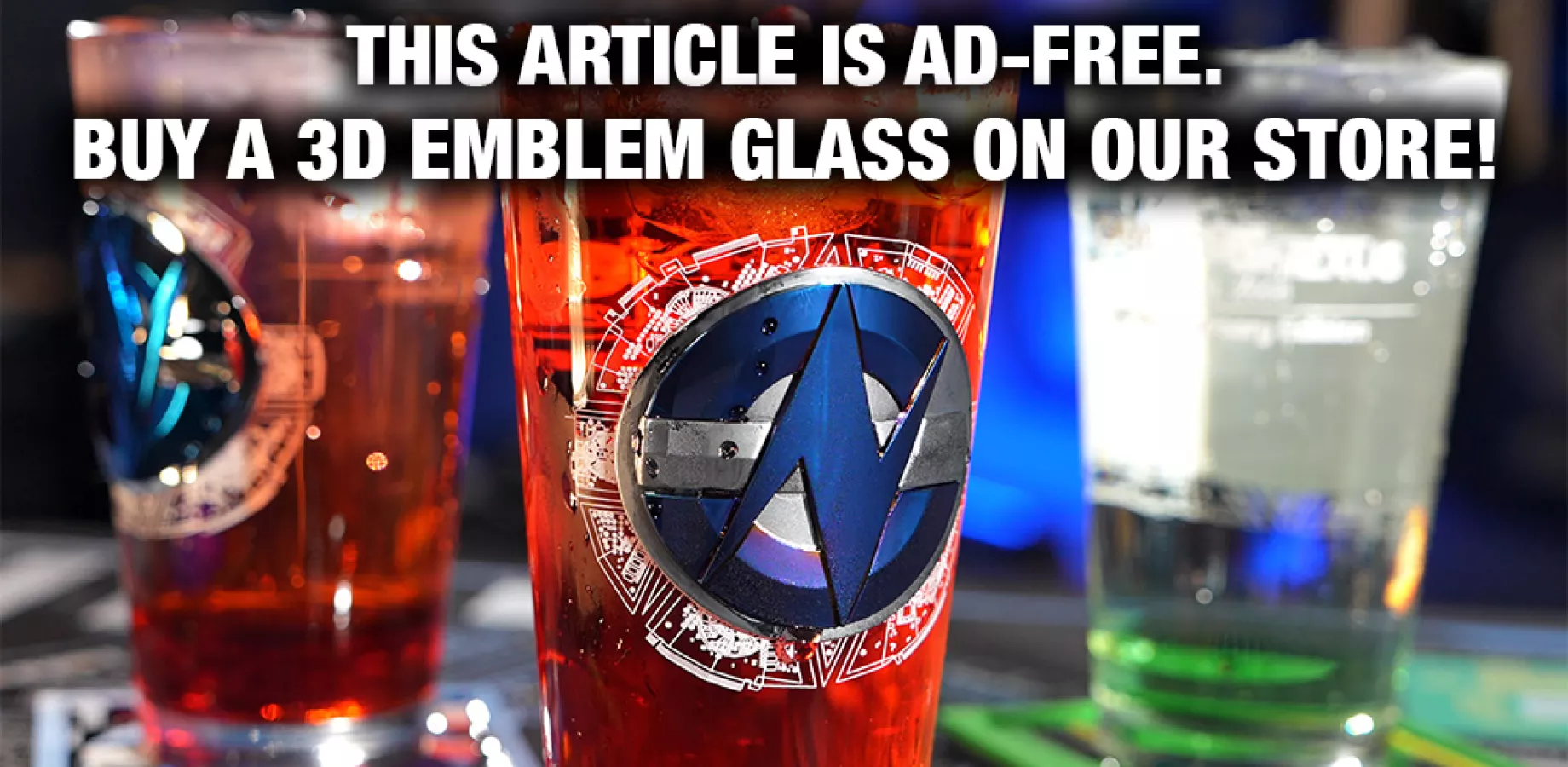
Coloring and Quality Control
Dye tank Dye vats Waste water return
Anodization doesn’t directly color aluminum, but it does provide a nice open porous surface for dyes to stick to--darker colors require a thicker oxide layer, and therefore more time to be anodized. The main production line only handles these two colors, black and white, as they’re the most popular. Other colors or smaller batches of parts are done manually in smaller tanks lined up alongside the larger ones. This factory offers thirty different standard colors--custom colors are also possible, but require much more effort. The dye tanks are held at 110C-160C, but take only about 15 minutes to preheat in the morning. Parts must be submerged in them for 5-10 minutes to be dyed. After coloring, the parts are rinsed three more times in water.
Every step of the anodization process requires large volumes of water, which must be replenished throughout the day. Anodization, as compared to painting, produces relatively low waste since the aluminum-containing byproducts filtered out of the water, like aluminum hydroxide, can be used by other industries and resold. The water drains out of a downspout at the front of the factory, and surprise government inspections to check the water quality are commonplace. We were told that it is easy to meet these requirements because the chemicals used are not too toxic.
After coloring comes QC. Color is checked against a reference to make sure it’s within an acceptable range. The most common defects come from parts moving around or bumping into things and damaging the finish. If the racks aren’t moved carefully, the parts can scratch each other. Smaller pieces are easier to deal with, while larger ones cause more problems. The factory can afford to be picky about blemishes because almost all defects can be fixed by re-stripping the oxide coating and simply repeating the process from square one, but if any serious damage has occurred, the parts are sent back. The customer sends in an exact number of parts for anodization and expects all of them to come back, so the factory must do its best to reclaim every defective part.
The final step is packaging. The factory doesn’t sell these parts themselves, so that means securely wrapping up the parts in bulk and delivering them back to their customers, like Lian Li.
As mentioned above, this is just one of several processes case manufacturers use for surface coating, depending on the requirements. Anodization is the preferred process for externally visible aluminum parts, but for a smoother and less expensive finish they use electrophoretic coating, or for vibrant and varied colors they use paint. Each of those processes has their own interesting differences.
Our factory tour playlist (that includes related processes like painting, electroplating, and electrophoretic coating) contains over 20 factory tour videos in Taiwan and China alike.