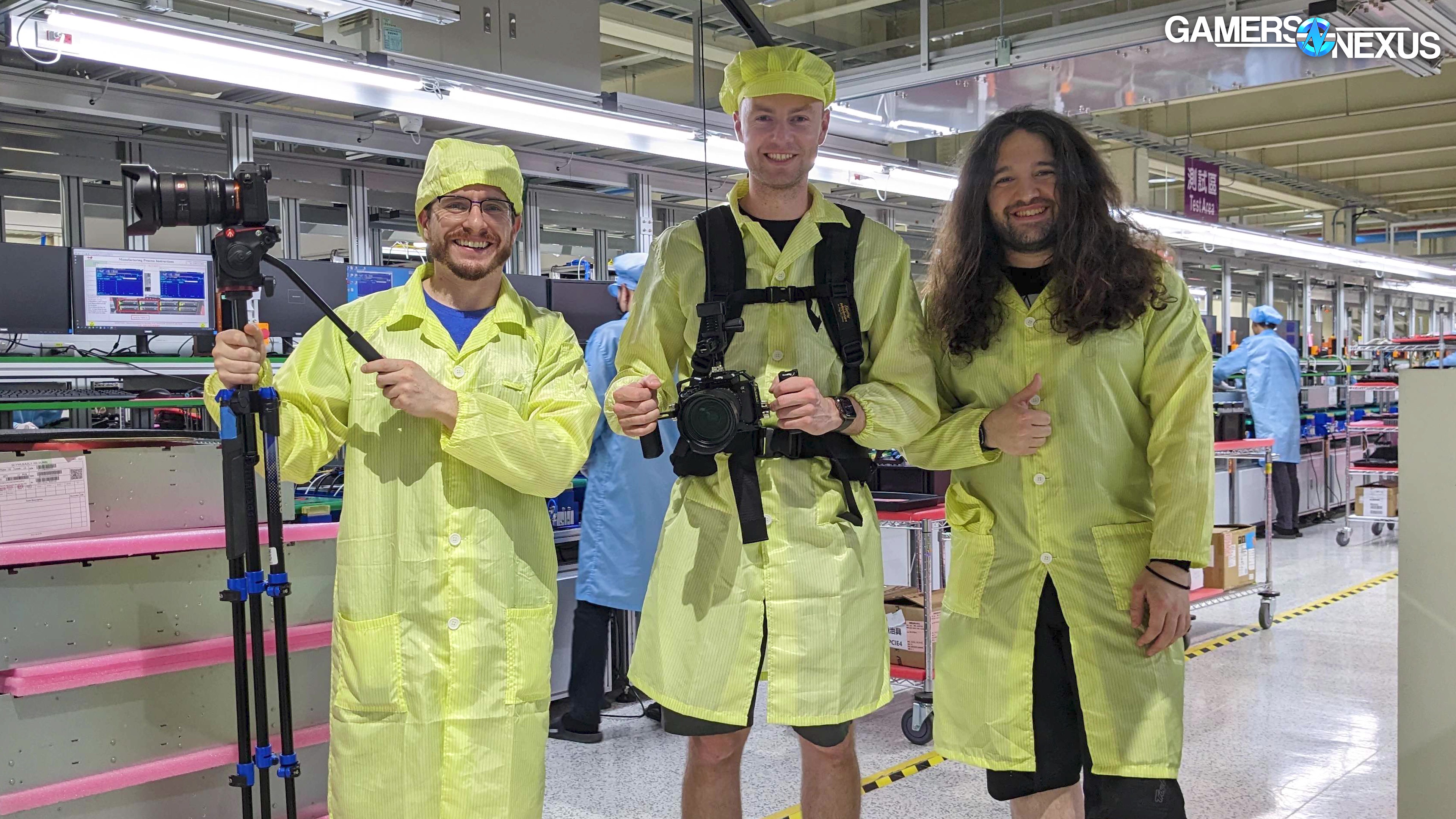
HUGE Computer Server Factory | Watch How It's Made: Cases & Servers | GN Factory Tours S3E1
Last Updated:
Take a look at how InWin manufactures, assembles, and ships its cases and servers
The Highlights
- We take a look at InWin’s oldest factory along with its newer clean server and system factory
- Factory workers are getting better access to modern safeties, but still contend with hotter and louder conditions
- Automation is increasingly becoming a bigger part of InWin’s production line, but physical labor is still a large component of the company’s workflow
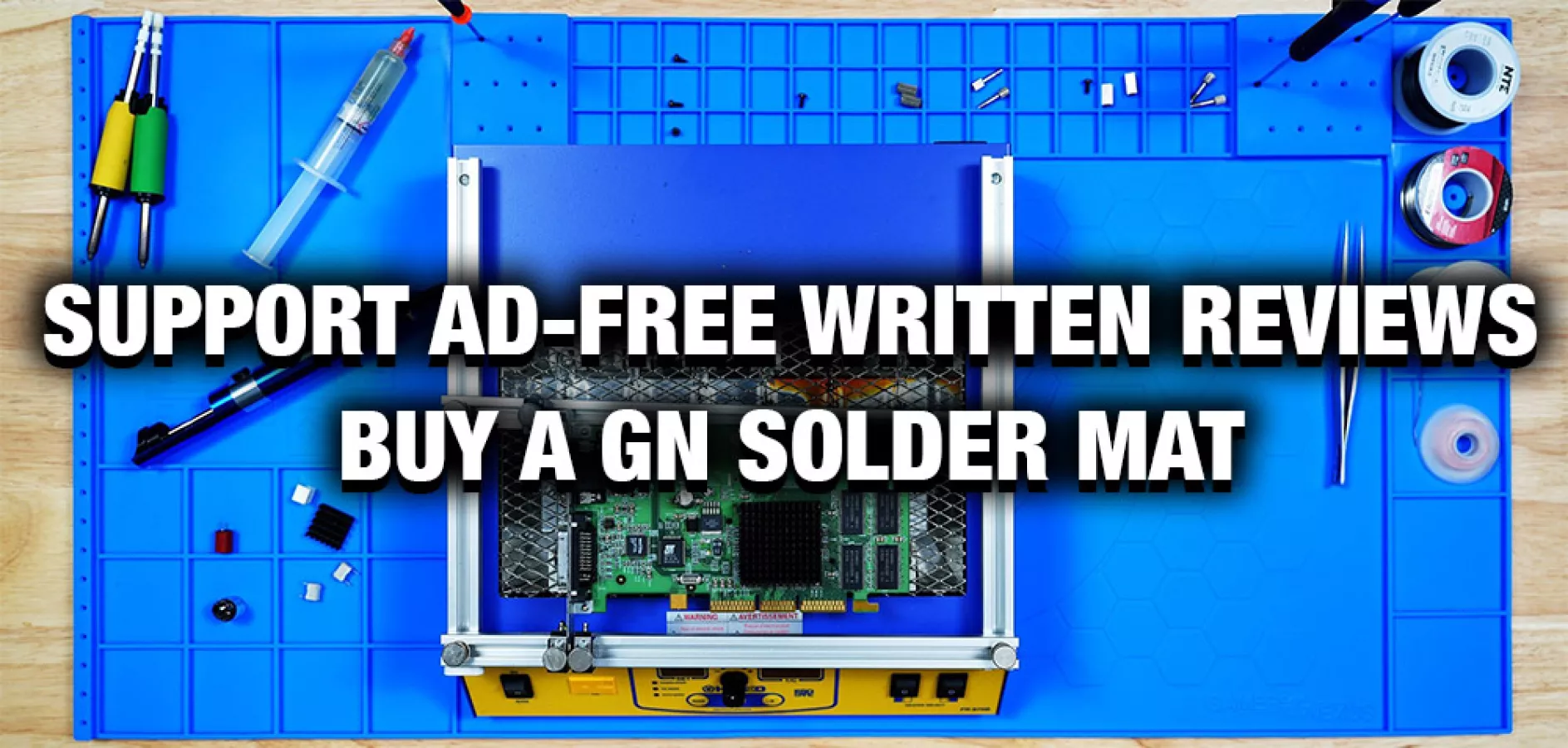
There are two very different approaches to manufacturing computer parts and servers in Asia’s sprawling mega factories: There’s the neurotically clean and obsessively sterile style of assembly and then the more traditional approach to manufacturing. In this article, we’re going to be looking at InWin’s case & server factories. Regardless of where you buy your chassis, the cases you purchase are made in places just like InWin’s. They’re grungy, dirty, and oily, and built for efficiency. We’ll be looking at InWin’s oldest factory and its newest in this tour.
The company’s cold-blooded efficiency gained from handmade customizations is what earned InWin the industry position and the money to make its clean, new, and nearby facility that we’ll take a look at first. The company’s clean server and system factory has hundreds of people work to bring the product from metal stamping down the street to its server assembly stations.
Credits
Host, Writing
Steve Burke
Video Production, Camera
Vitalii Makhnovets
Camera
Mike Gaglione
Writing, Web Editing
Jimmy Thang
Server Assembly Line
Pictured below is a server, delivered freshly assembled on an anti-static platter. These servers are built in a brand new factory for big clients we can’t name, but your web traffic has probably ended up on many of them.
Each server is not only built here, but tested too. And the testing process sounds like a jet engine.
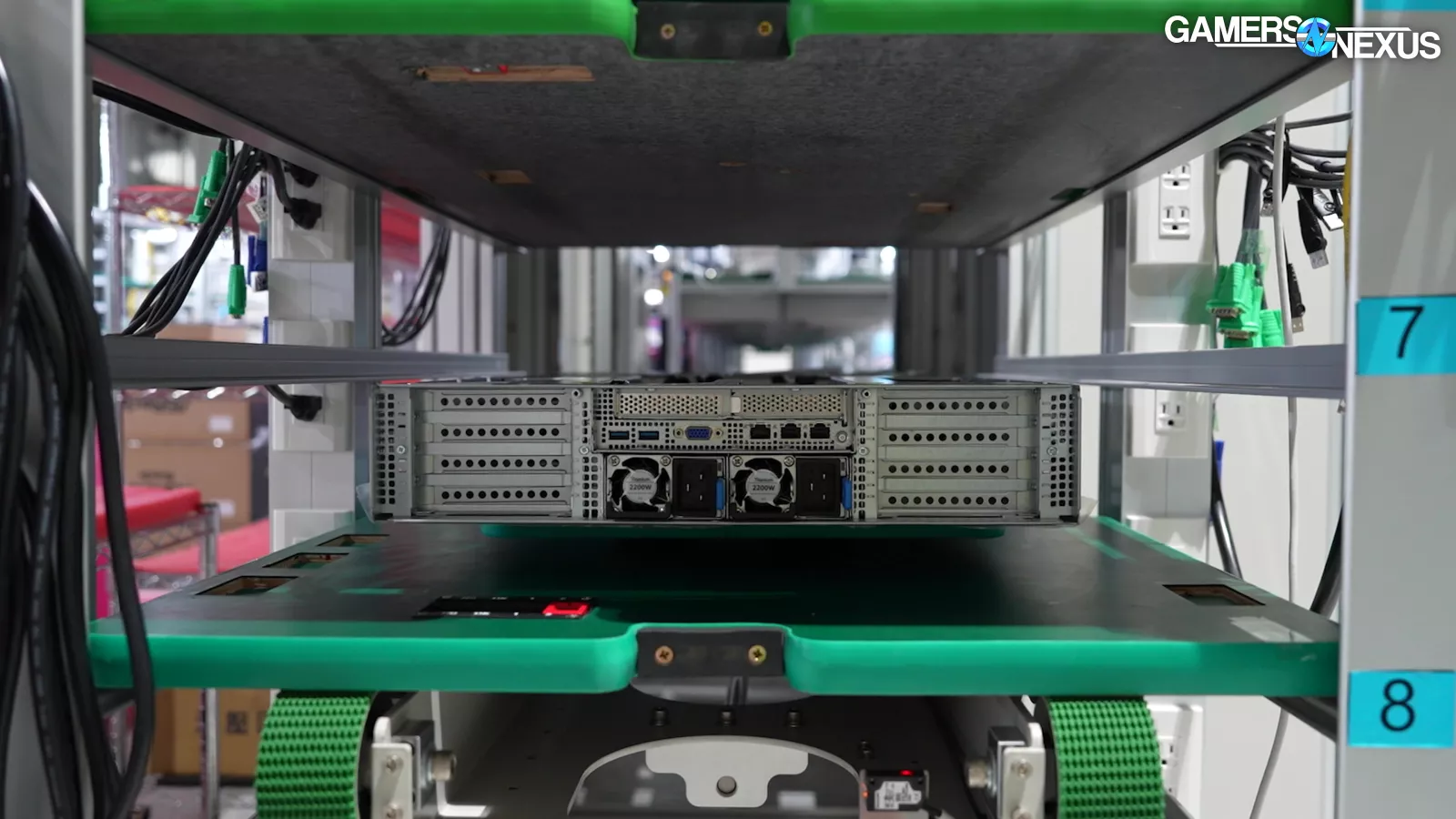
We started our InWin factory tour in the assembly line which, just by price of CPUs and RAM alone, is probably one of the most expensive areas per square foot in the city of Taoyuan, Taiwan.
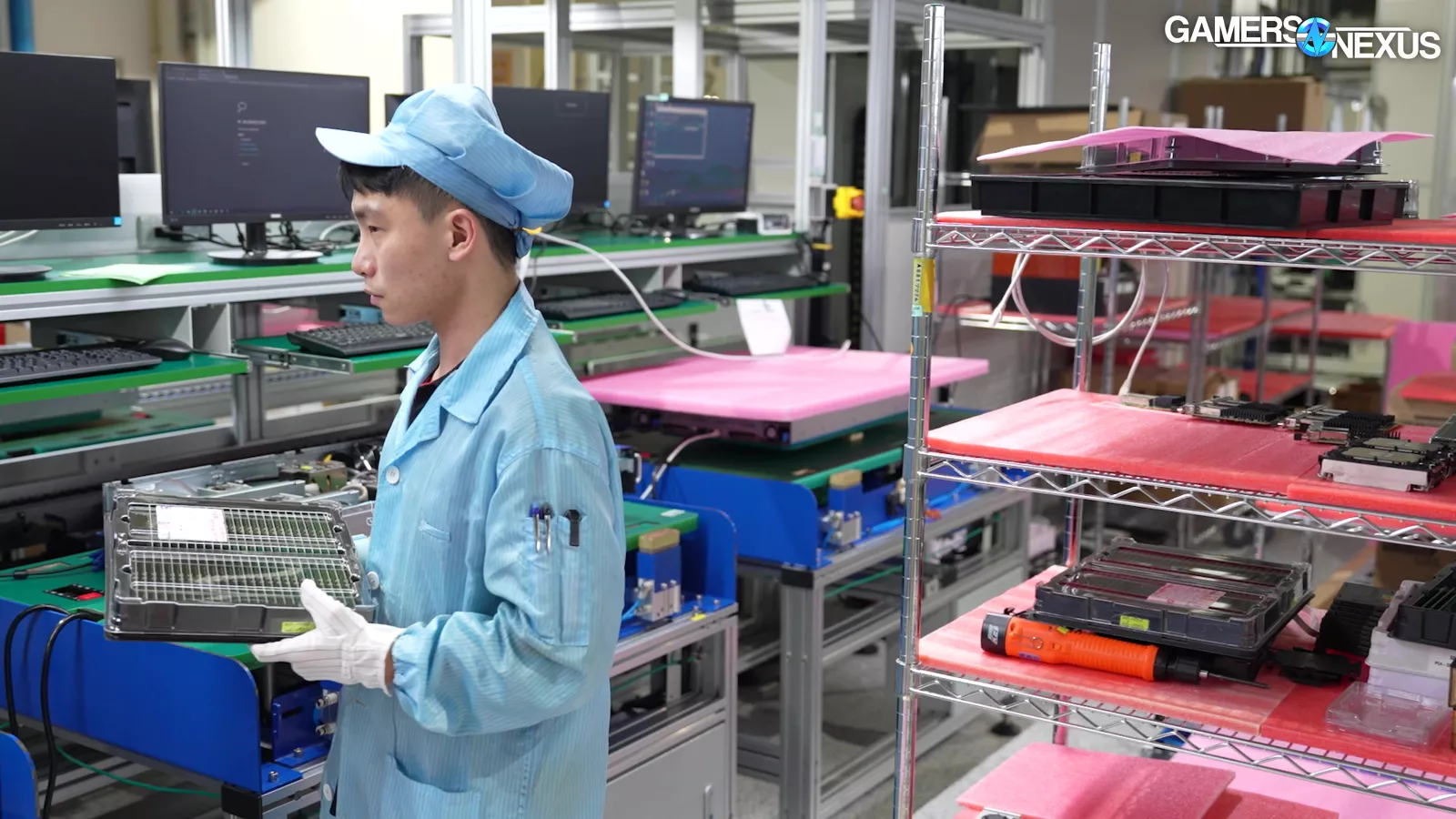
Technicians take trays filled with terabytes of RAM and multiple AMD Epyc or Intel Xeon CPUs over to the conveyored workstation.
From here, the technicians check the build order on the screen and start assembling the actual components of the server by hand. The cases are made down the way by an InWin factory that we’ll talk about later -- and actually, we’ve covered in the past.
There are 6 complete lines per floor at any given time for assembly, with each featuring its own SOP for the customer orders. Per day, this factory can turn through about 80 servers per line, maxing out at about 480 servers for this floor alone.
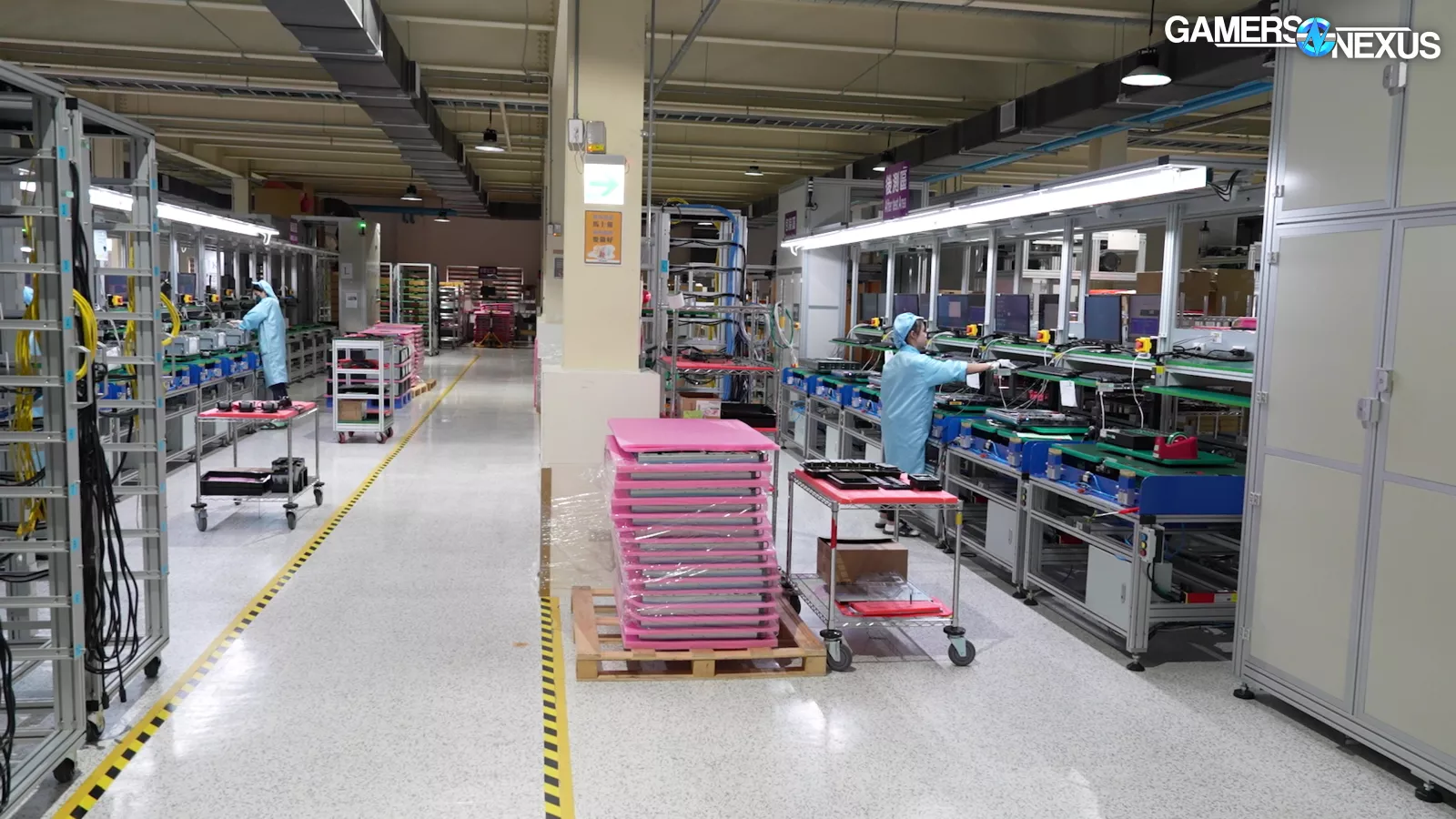
A different line is configured for 2U systems due to changes in process. For full configurations with maximized RAM, an assembly line crew might socket upwards of 1,000 sticks per day. We’re betting the job application asks how strong your thumbs are.
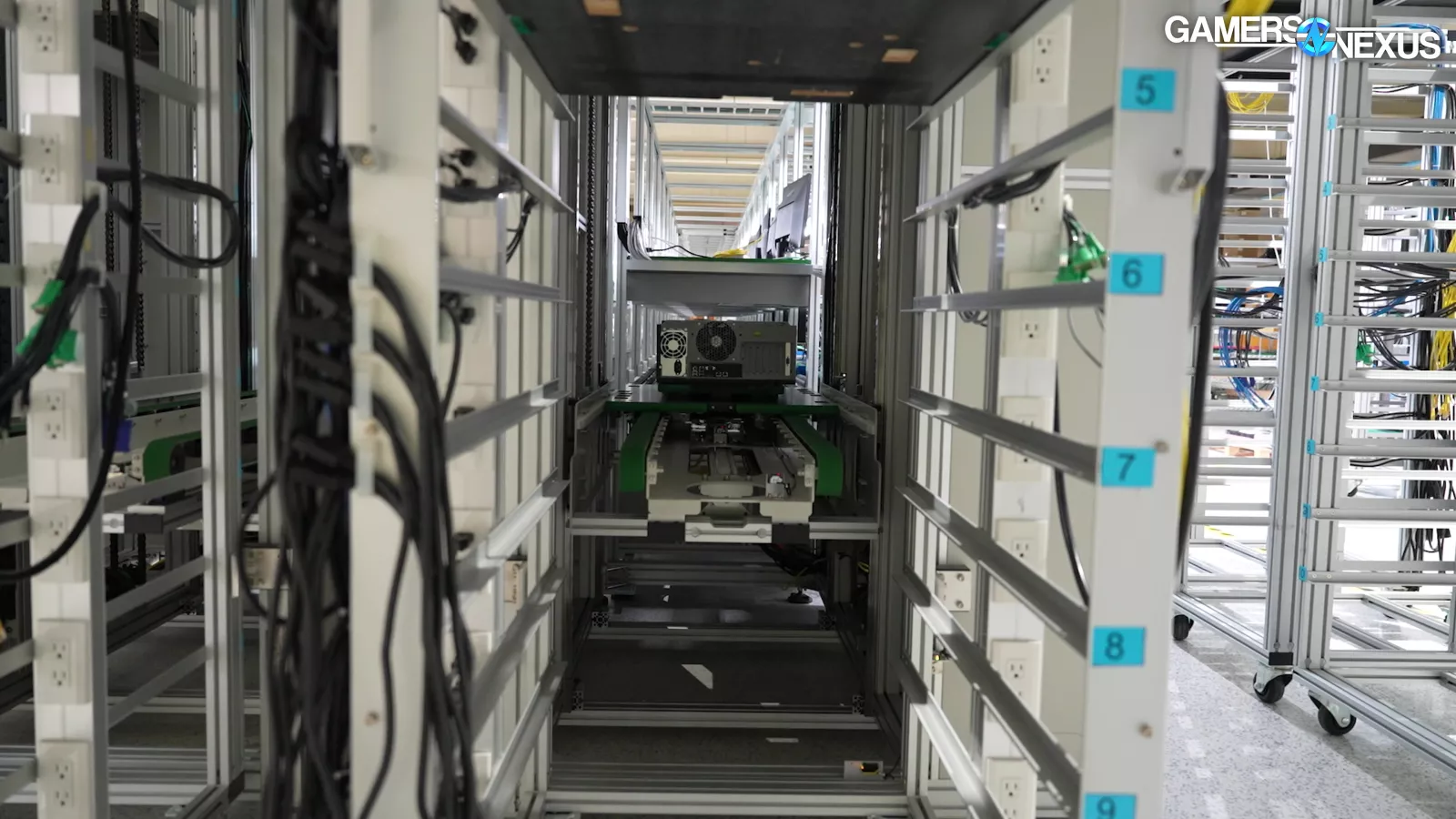
As the systems are built, they are automatically carried down the conveyor belt and moved station-to-station. Eventually, the server is brought into a server elevator and brought out of sight.
But at GN, we’re still developing object permanence. So we asked the InWin crew to prove the server still existed once it left our sight. They told us we’d have to figure out a way -- and sometimes, that means we break the rules to get a shot.
Standing atop a pallet stacker, Steve held the position above for about 5 minutes to get the shot below as we waited for InWin to send a server across.
Until we realized something was lost in translation, and all they sent across was an empty turntable that a server would normally be on. Well, good enough.
Server Testing Facility
After the machines progress through this conveyor maze assembly line, they make their way over to this ginormous, high-power testing room.
Up to 800 1U servers get burned in just in this room alone. As for its power capabilities, the room is equipped with 80 total test lines, each capable of delivering 5,000W. The total power handling capacity of the testing floor for the factory is a staggering 400kW.
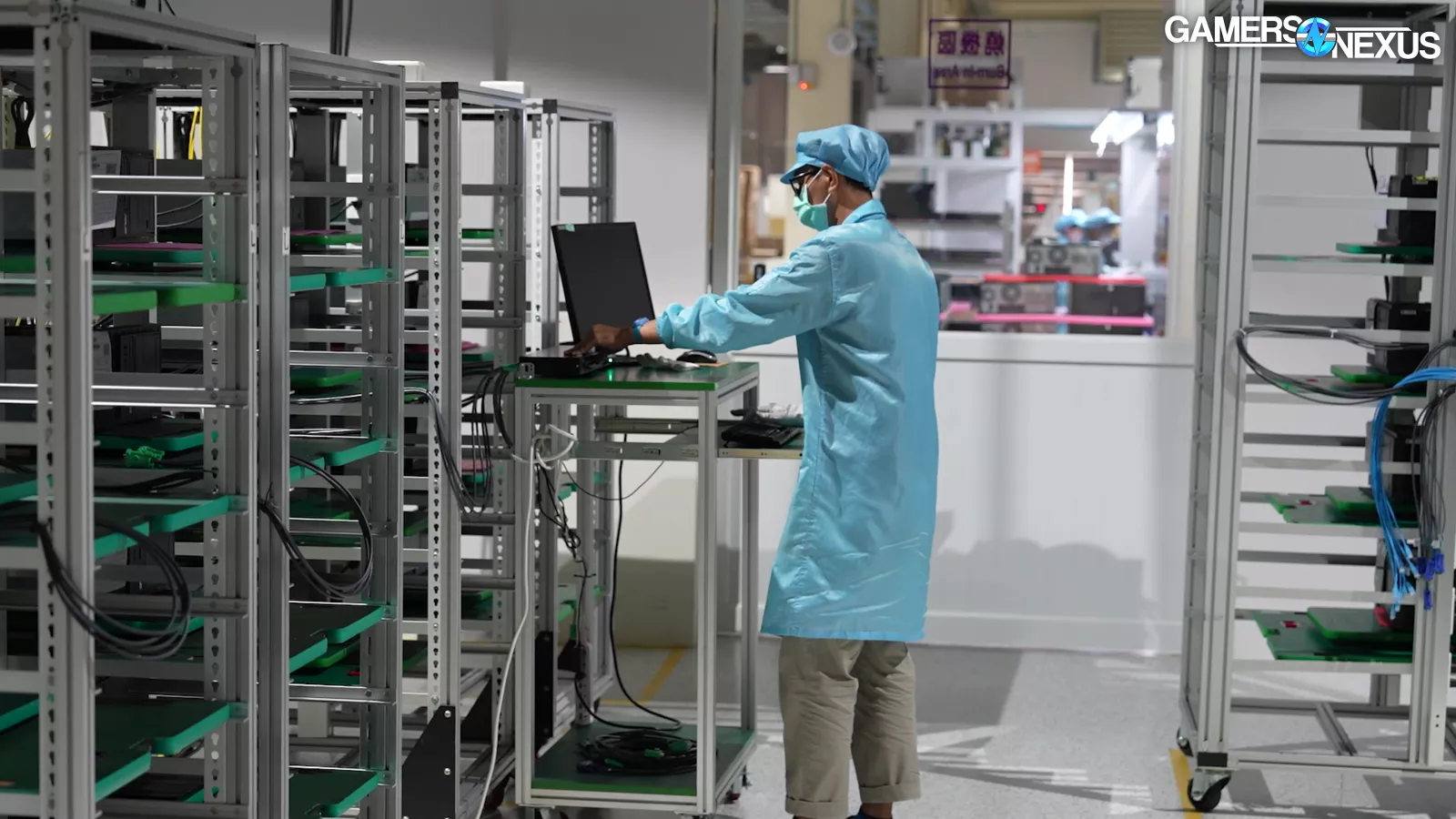
Total burn-in time is 2 hours per server at 10 units per rack. And one guy controls almost all of it -- meet the man with the most powerful index finger in the world, trained from entering BIOS hundreds of times per day.
The test racks in this area cycle through I/O testing to make sure all ports fire, CPU burn-in, cooler burn-in, and even testing the entire RPM range for the fan. And it sounds kind of like a deafening aircraft carrier when they all fire at once.
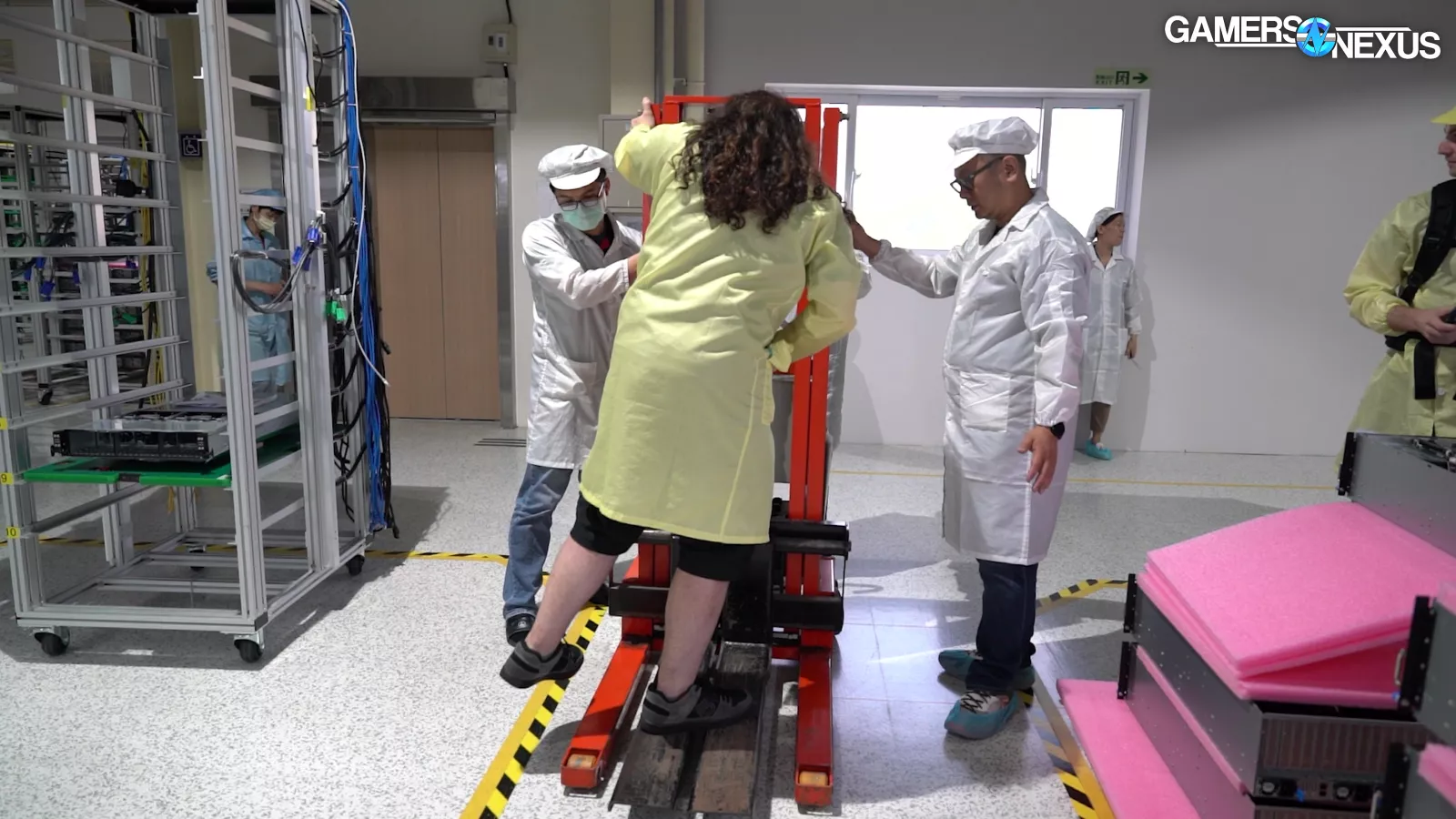
And no, OSHA doesn’t exist here. That’s also why Steve was allowed to climb the pallet stacker.
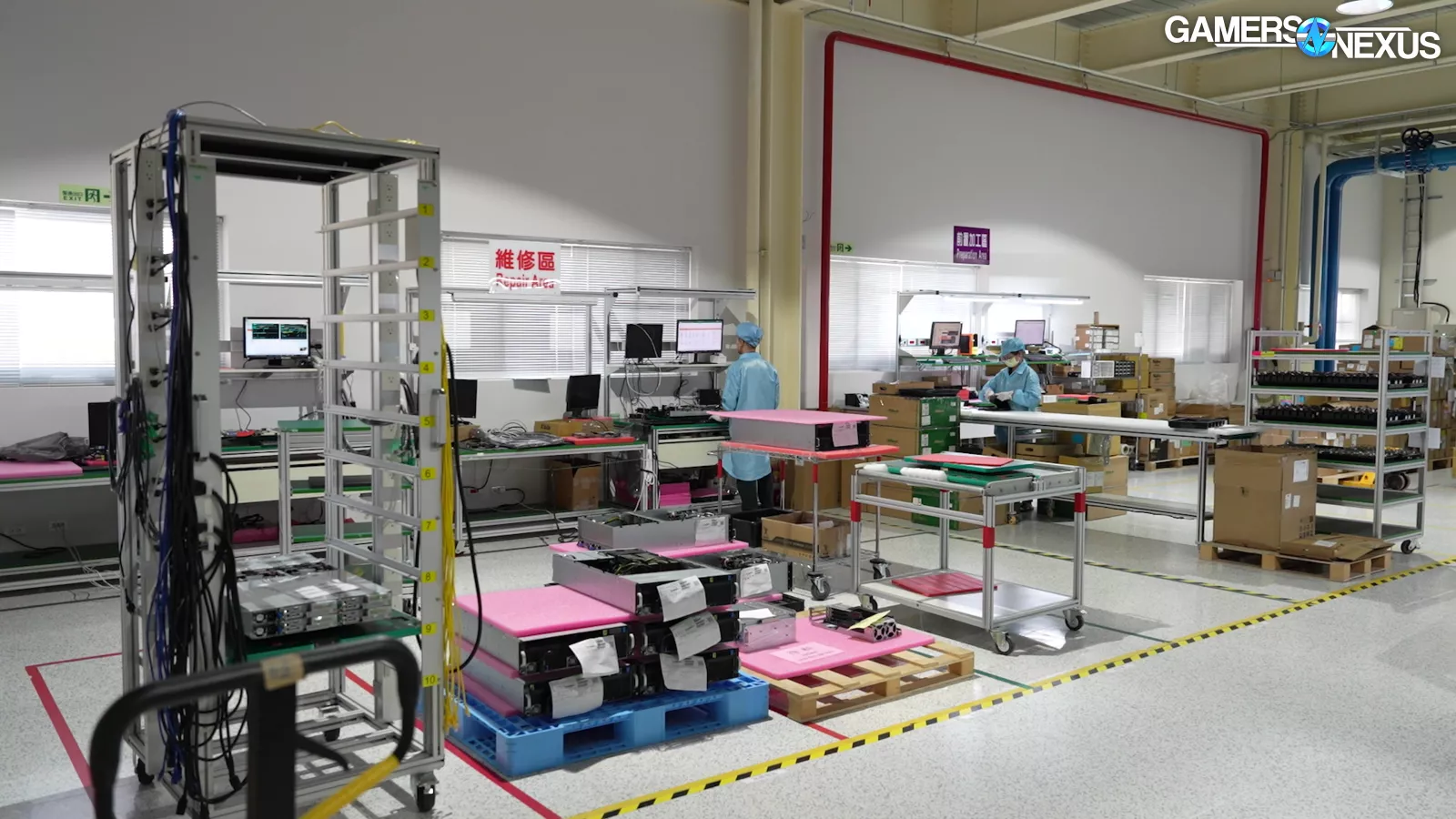
The testing suite is largely developed by the factory itself, with software designed to alert technicians to bad components or test failures. Anything that fails goes to the repair station, where technicians will identify the bad part and rescue the rest of the server. Some bad components, like sticks of RAM, can be sent in for board-level repair by the original supplier -- especially since many of these factories are local to Taiwan, making it logistically easy.
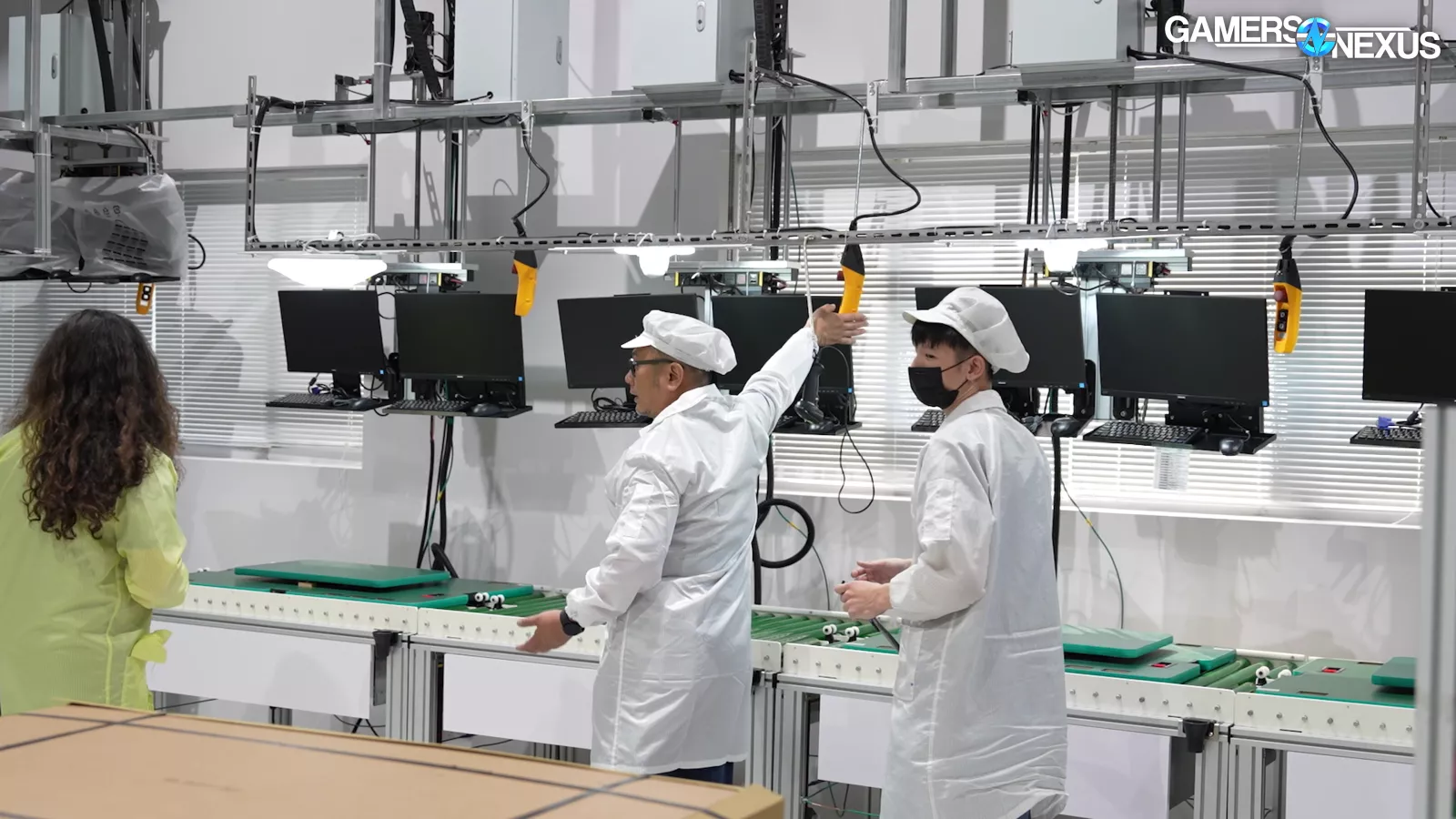
Other testing is done in a side room for low-volume custom builds.
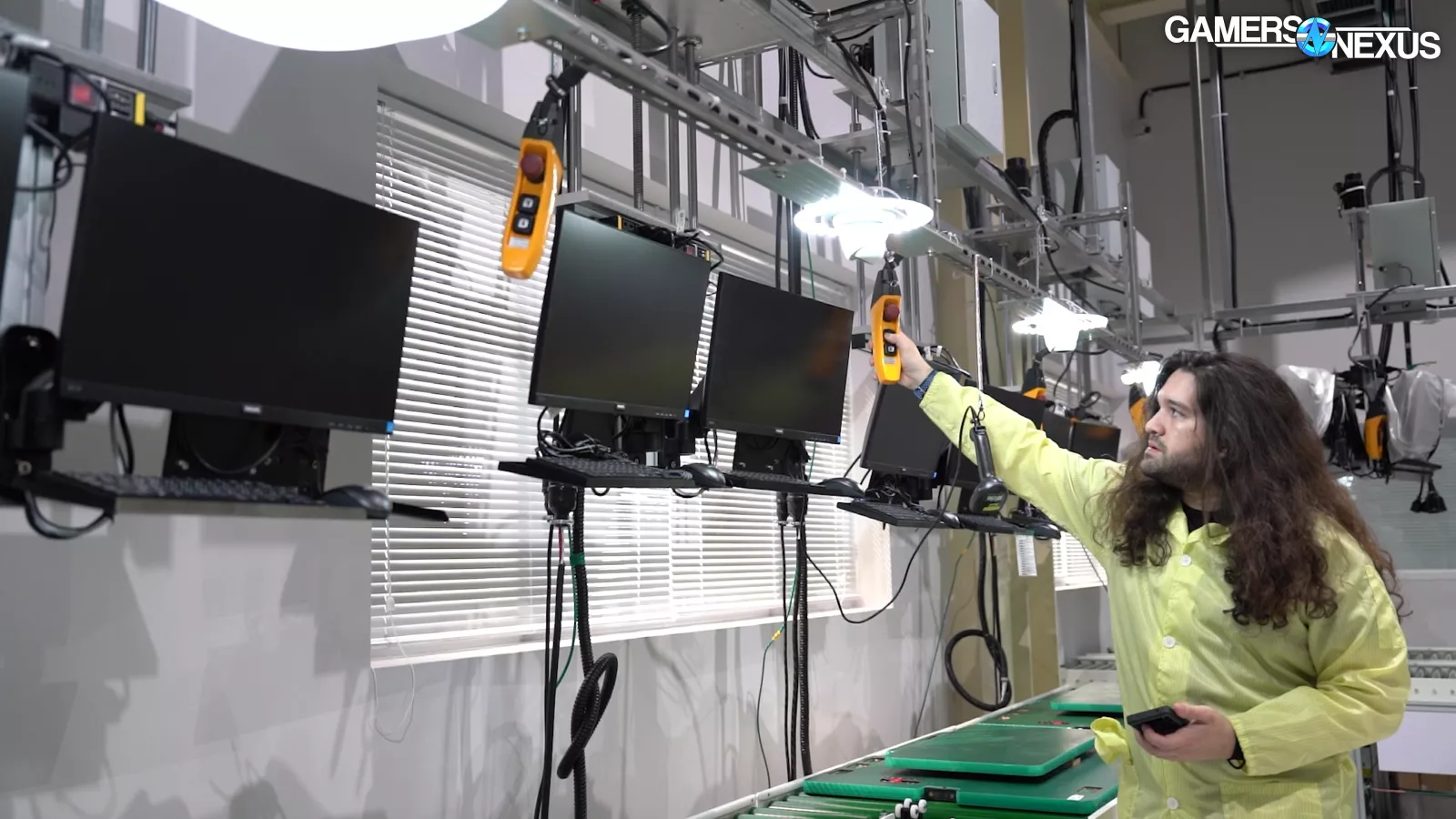
Steve was briefly assigned a job he couldn’t possibly screw up: Move the monitors up and down with a button. These stations are also used for documentation and photography to keep a record of serial numbers and parts.
The servers are loaded onto pallets when testing is complete, then prepped to move to packaging.
Water Cooler Testing
There’s one more secret room before we go to packaging, and it’s pictured above.
This brand new facility is for water cooling testing on servers. The huge amounts of perfectly installed plumbing in this room allow for up to 38U or 20KW of servers to be tested at once.
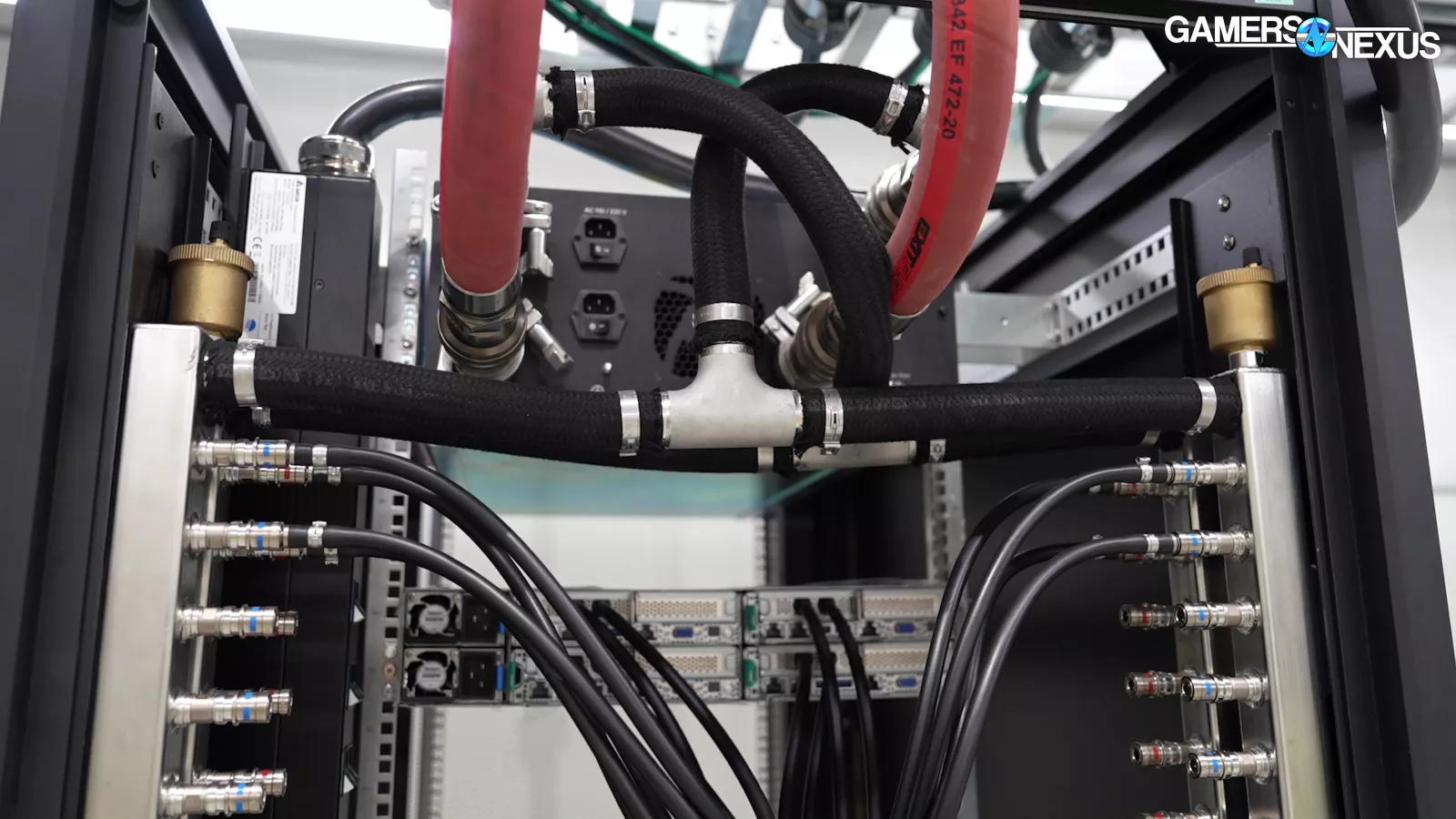
The water pumps through these huge hoses, with pressure gauges placed throughout to help check for leaks. They’re also checking the water temperature here. This can be configured to test water cooling for entire server racks -- or multiple -- for complex systems.
Or they can test a single unit at a special station, pictured below:
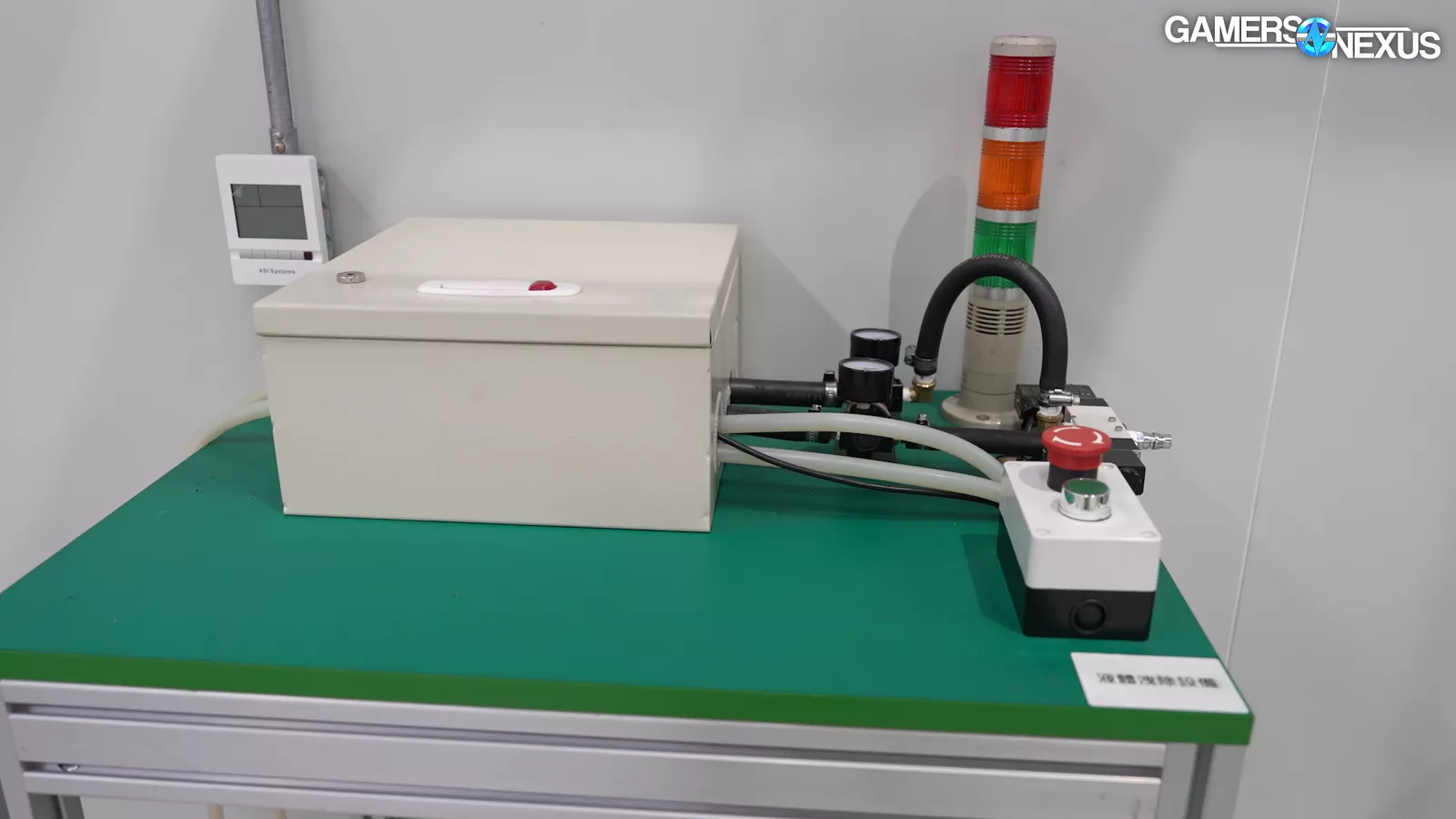
All the water is pumped up to a giant radiator and set of tanks on the roof, which we were able to capture with our drone shots:
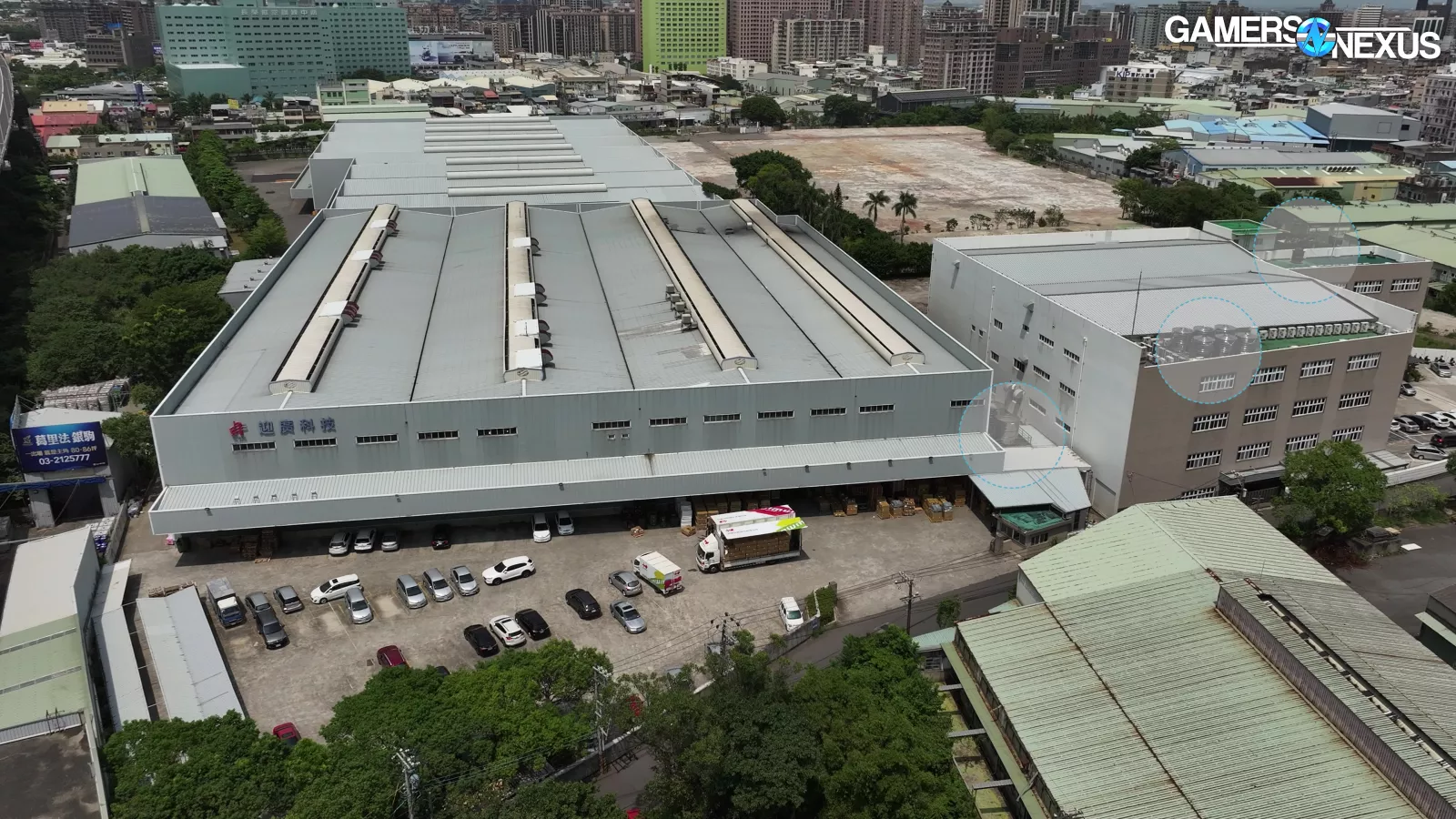
Packaging Robots
After this entire process, everything goes to packaging -- which is a whole beast on its own.
The images above showcase the packing station. Here, pallets upon pallets of servers are unloaded onto conveyor belts.
A technician screws all the panels together, then performs final quality checks and inspection for all components.
A team manually packs the servers into foam and boxes.
Despite being maybe one of the least sophisticated parts of this factory, the automation around a roll of tape is surprisingly satisfying: Each box gets auto-taped, rotated, and taped again, and although we couldn’t name any of the clients earlier, there might be hints in the image above as to who some of them are. But we’re not sure...
Continue reading below to see the grungier painting factory.
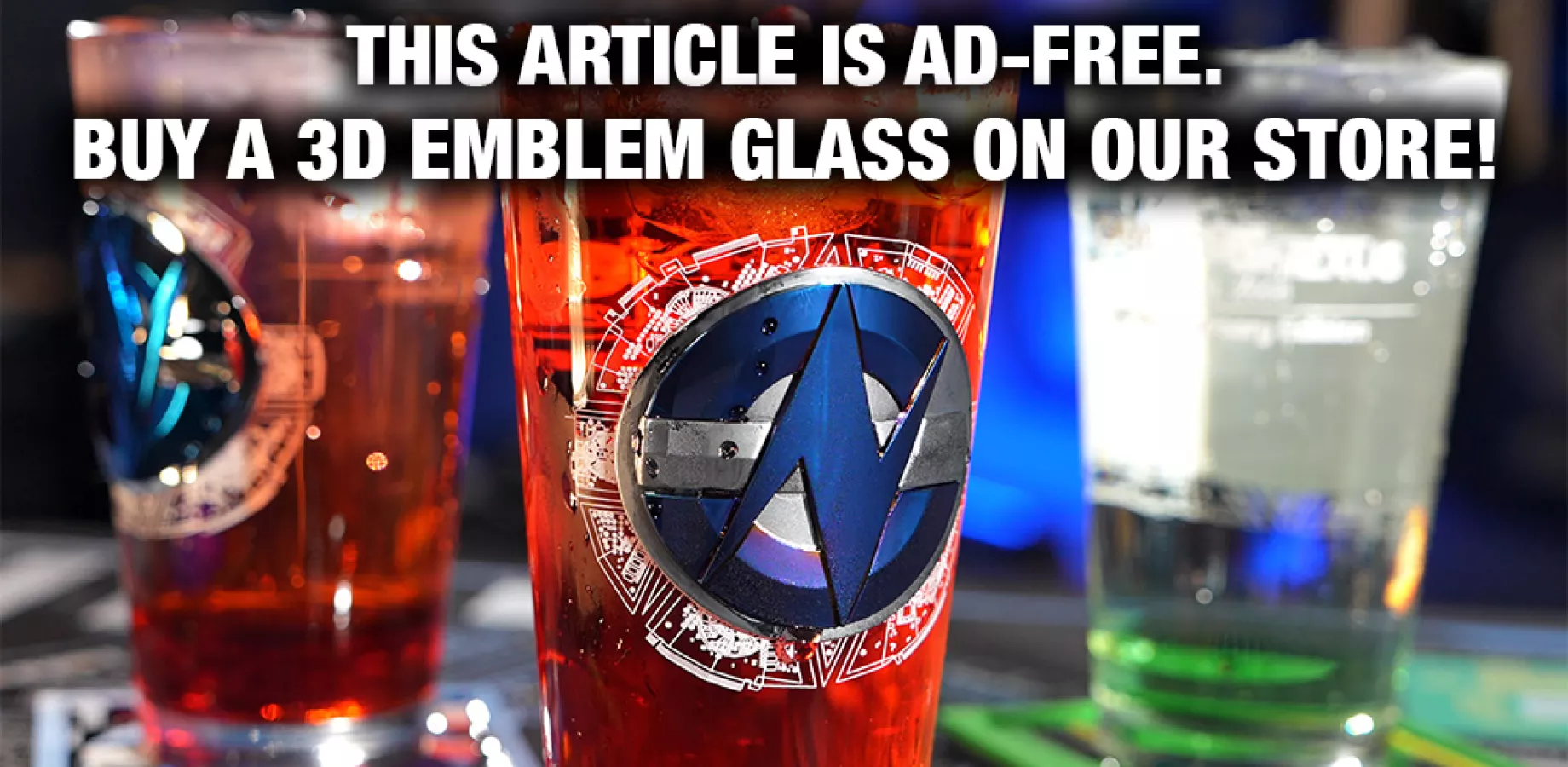
InWin Case Factory & Painting
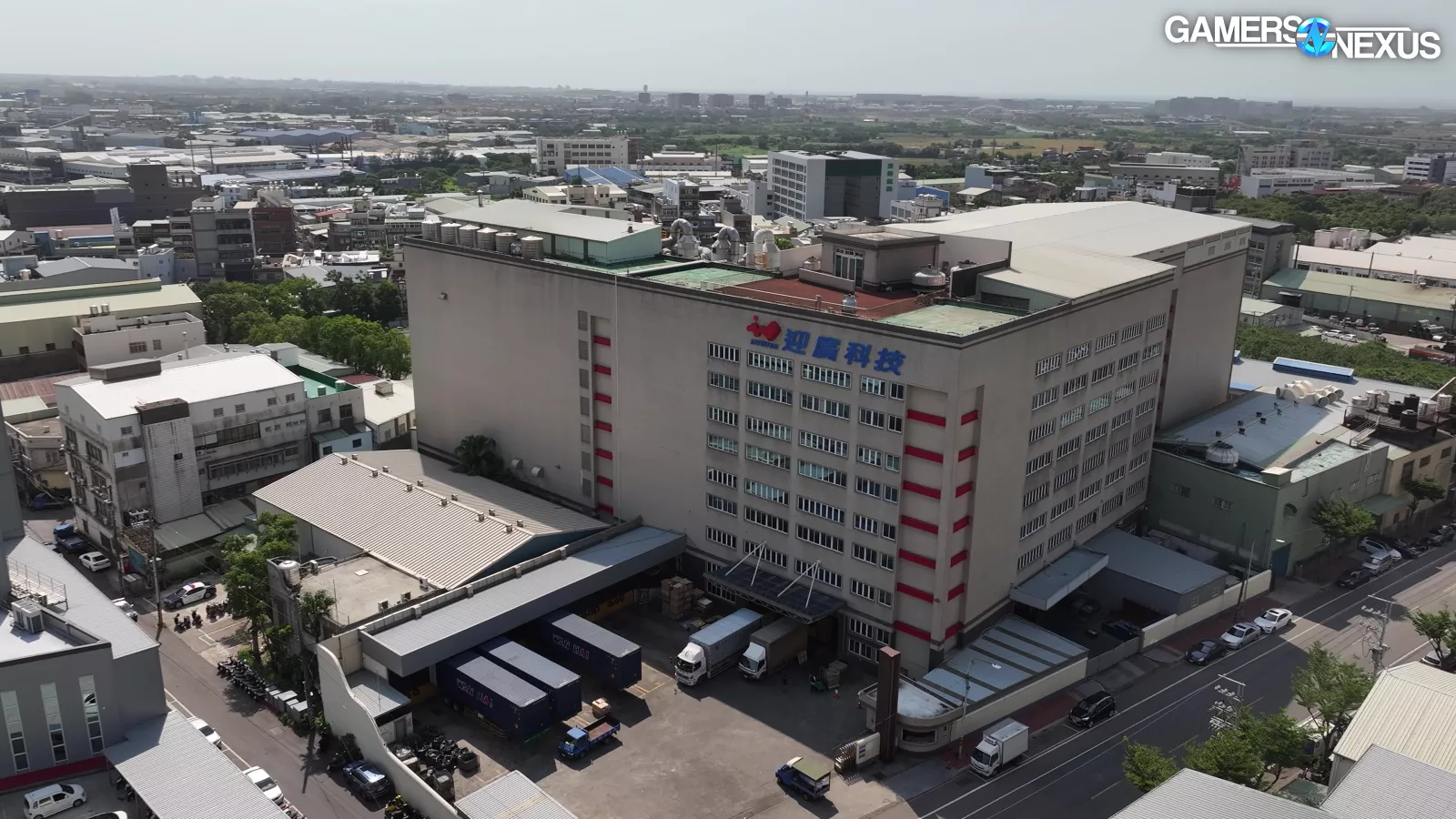
A quick car ride away, just down the street, is InWin’s longest-standing, traditional factory, which underscores some truth about factory life.
These floors are kept dark to help combat the heat and humidity of Taiwan combined with the heat of ovens baking cases at nearly 200 degrees Celsius.
In this old factory, cases are automatically moved along a ceiling-mounted conveyor line using hooks. One by one, the cases climb to get painted and then baked.
The walkways are crowded with machines and massive equipment -- the claustrophobic wouldn’t do well here. There’s also the everpresent sound of paint waterfalls surrounding this area.
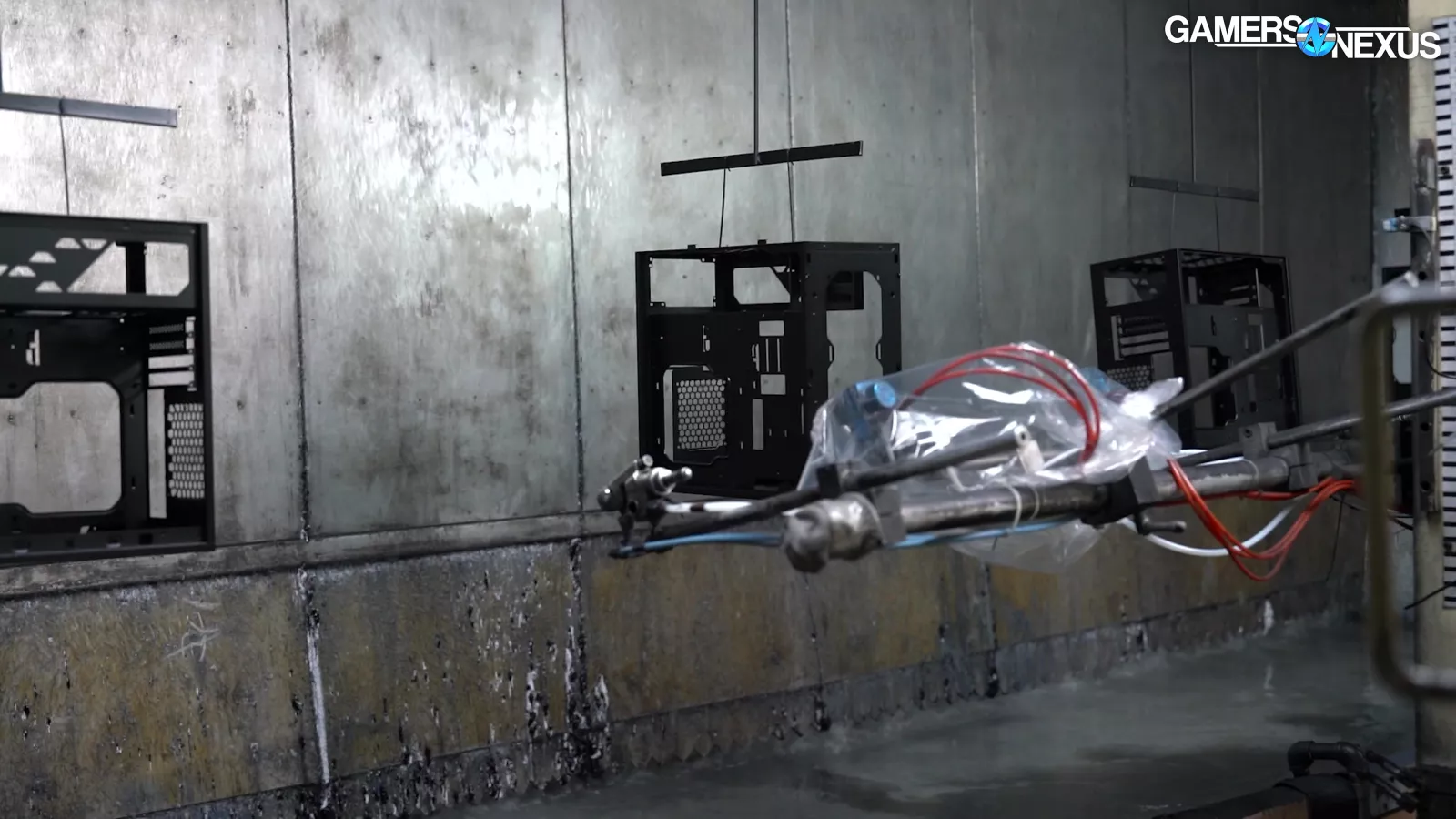
On the scale of factories we’ve been to, the presence of at least respirators is better than we’ve seen in some others -- but it’s certainly not conditions we’re used to in the modern West. Between the noise and the air of the many non-robotic painting factories we’ve been to, floor managers at various companies have told us that it’s been hard to keep staff around for very long.
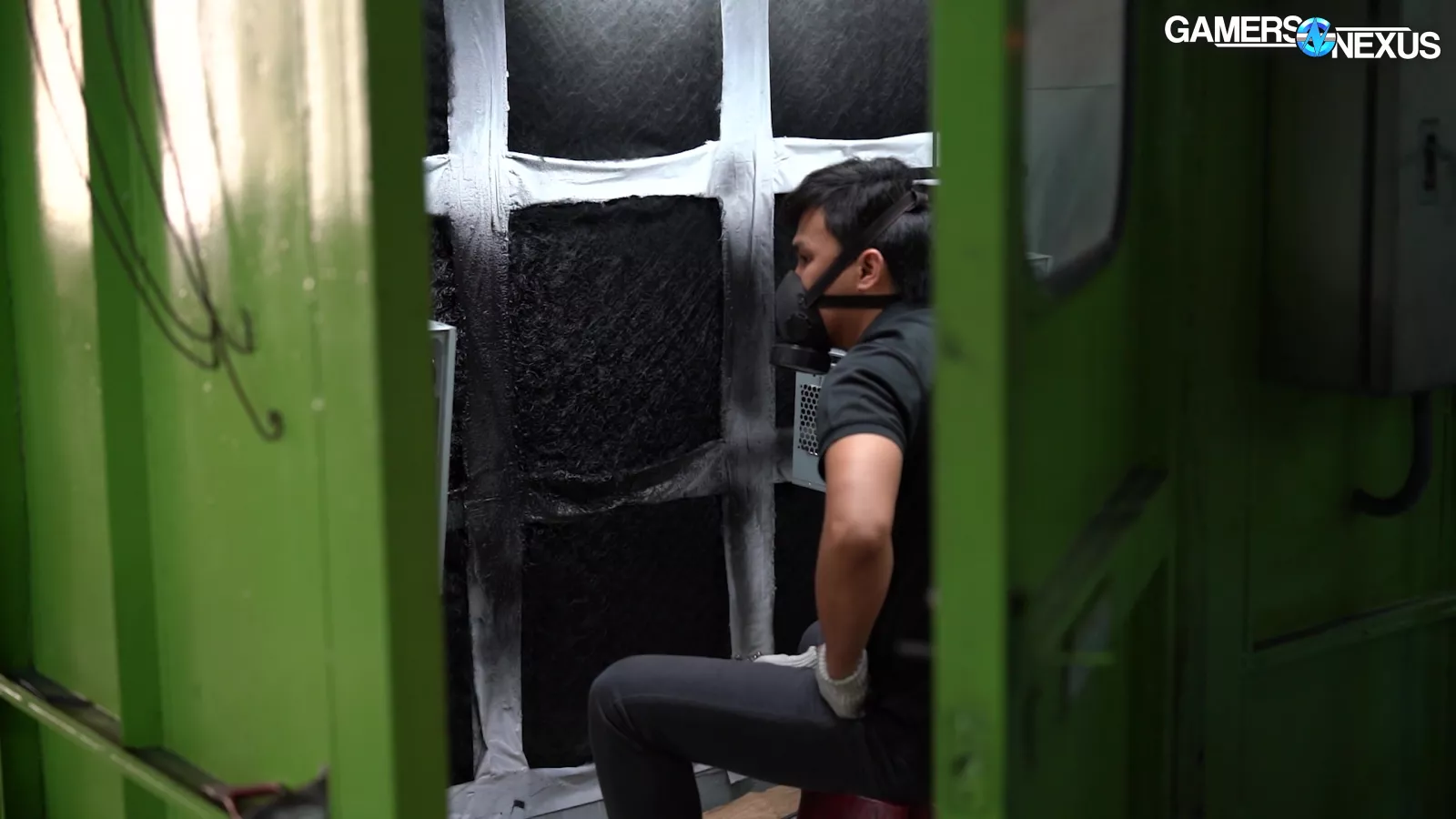
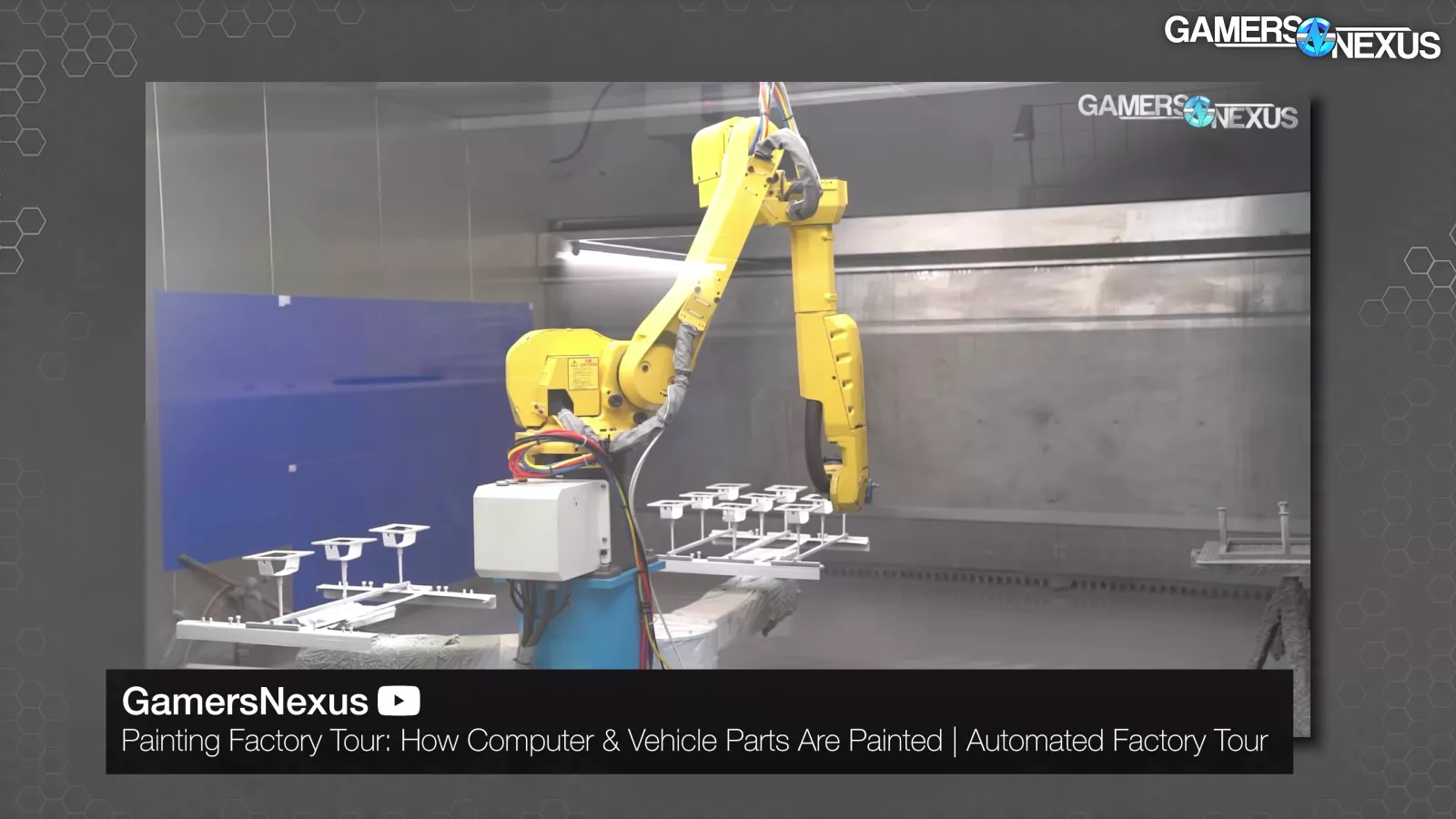
Robots have been slowly filling-in the gaps for this former manual workforce, as we showed in our previous automated painting factory tour. Maybe in instances like these, robots are for the best.
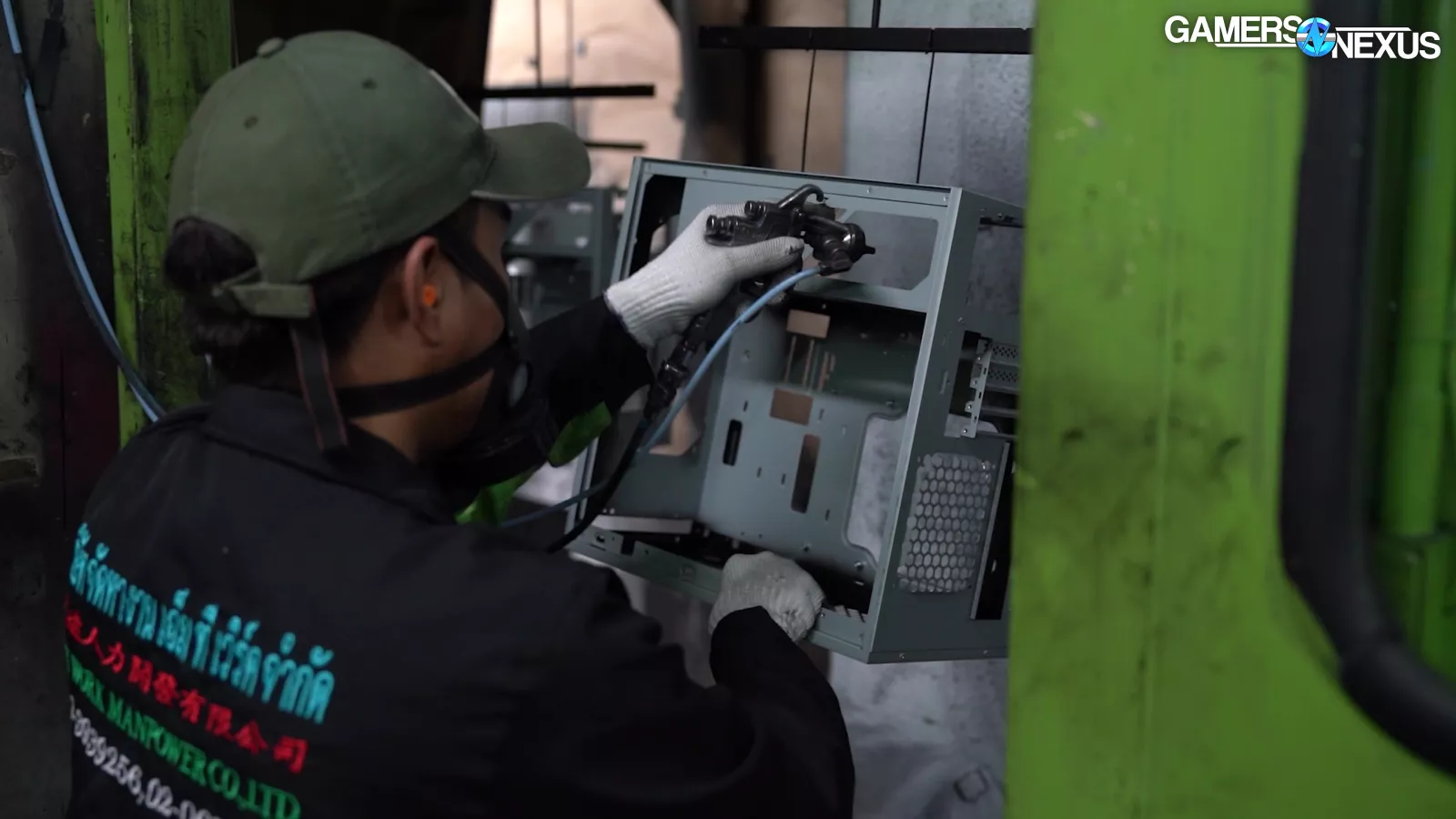
Workers prep the cases and paint them as they’re carried from one paint booth to another. The hooks are mounted in a way to minimize obstructions to the paint, workers manually mask some parts of cases, and they’re brought at a fixed pace through the painting process. Later in the process, more automation is introduced for the generalized coatings, whereas the earlier manual processes focus on hard-to-hit spots.
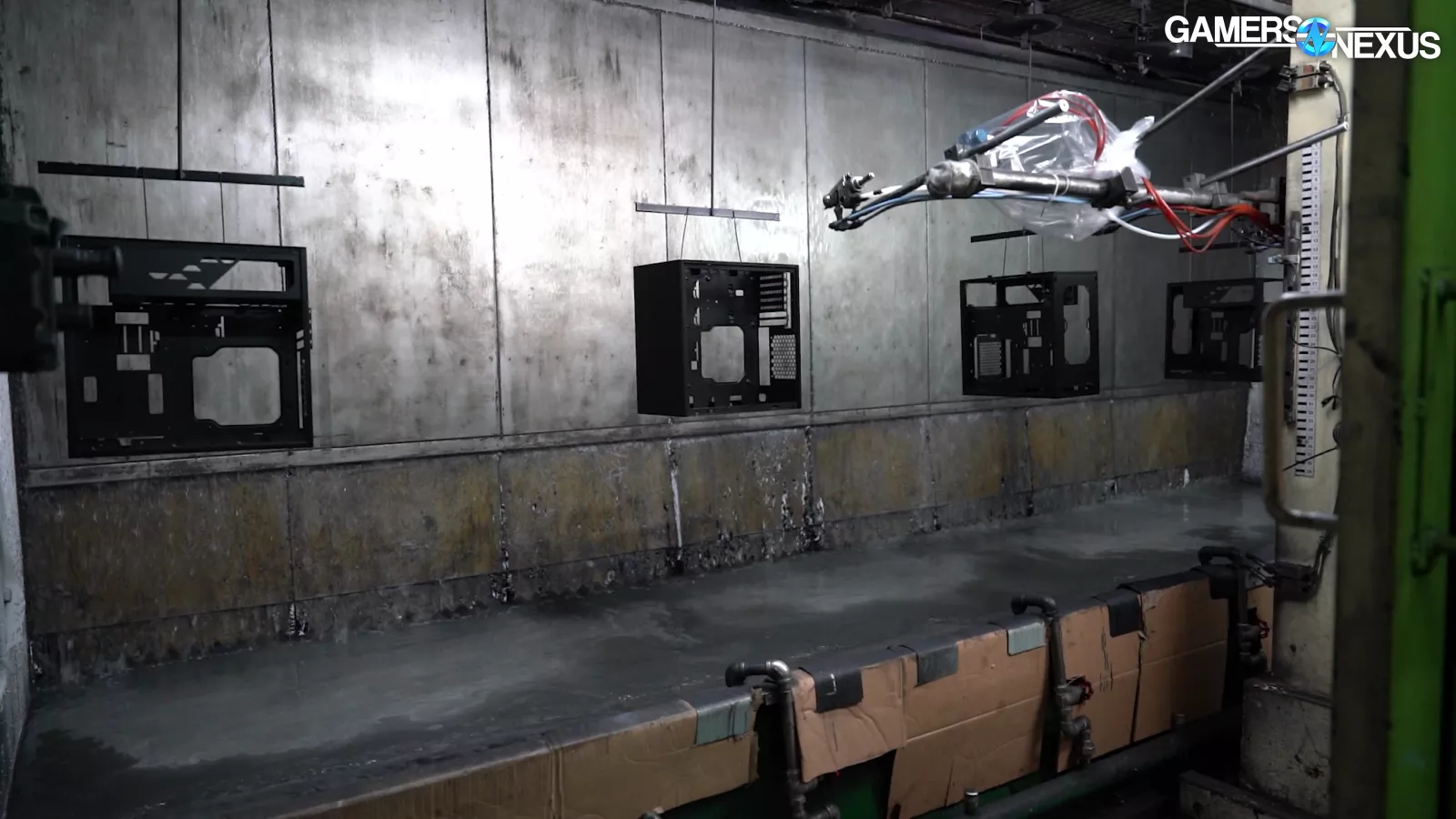
These waterfalls help wash the overspray down into a catch basin mixed with paint and water, amounting to millions upon millions of liters of use annually. The factory is able to recapture and reclaim much of the water and squeeze the paint out -- which is something we showed in a prior Lian Li painting factory tour -- which reduces usage.
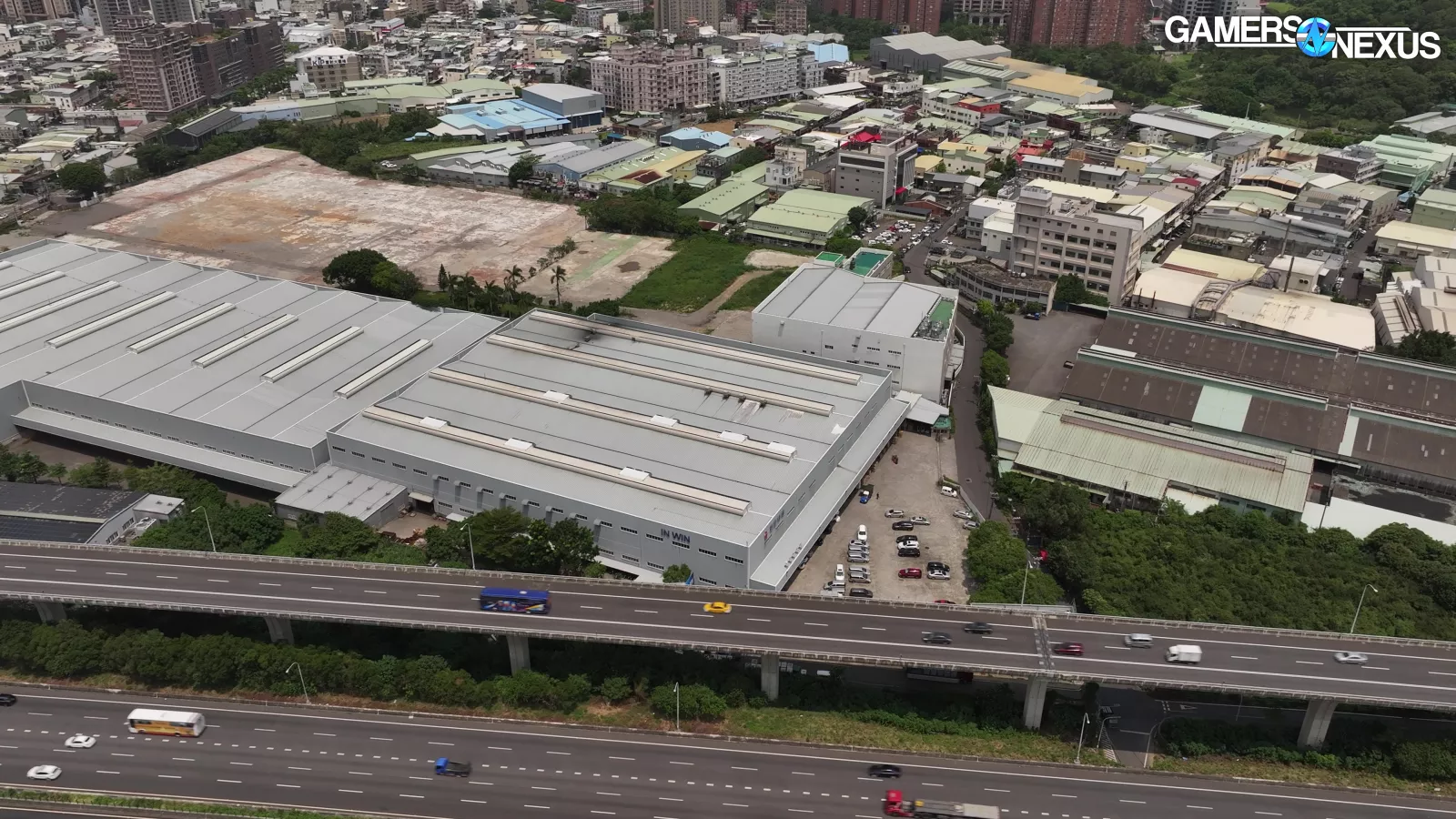
Pipes are exposed outside of the building that allow the Taiwanese government to perform unannounced audits of the filtration quality.
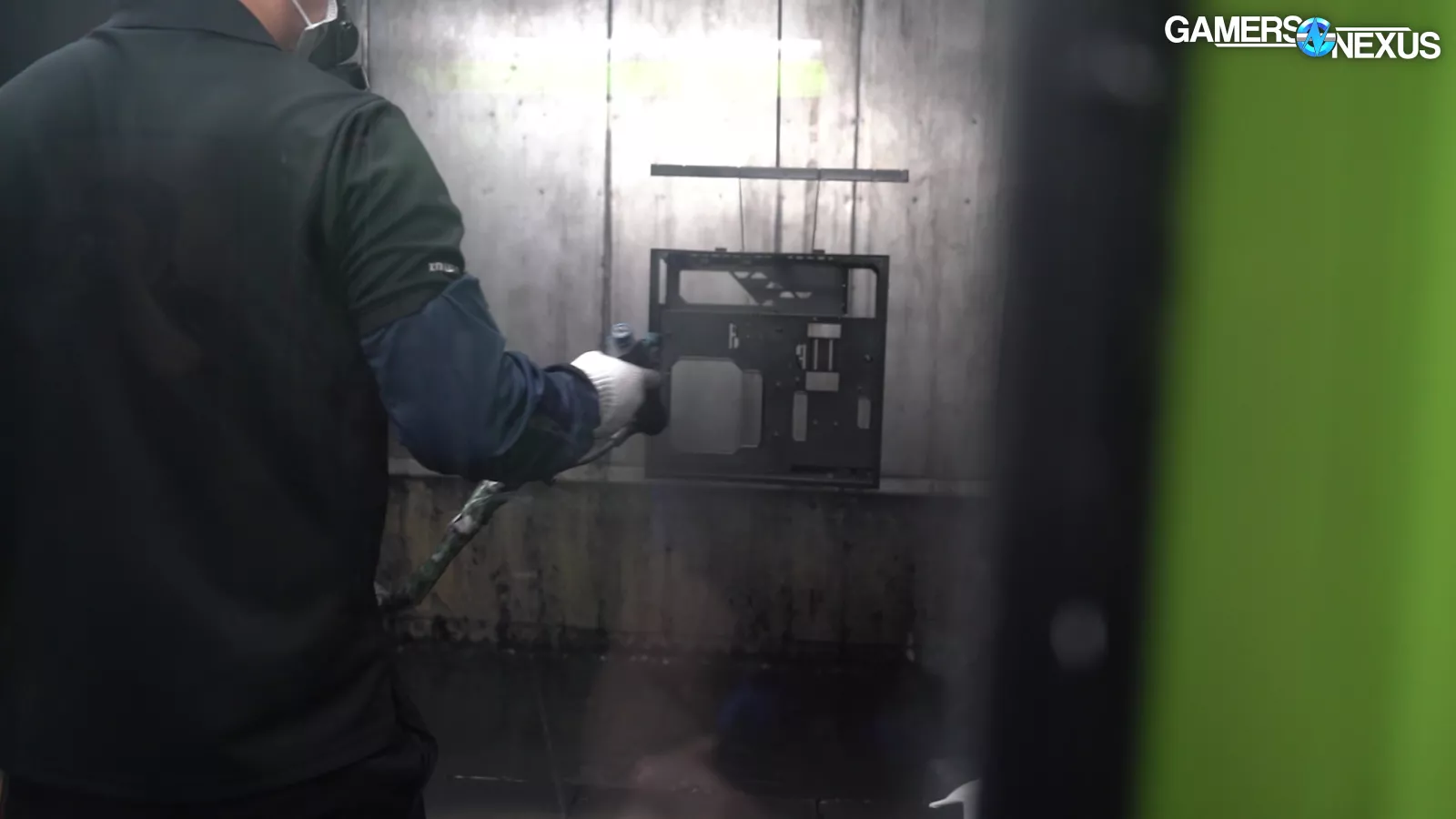
The entire painting process for each case takes about 40 minutes, and the baking process starts first at 75C to slowly harden the shell, then ramps to 180 degrees, and finally 200 degrees for powder coating.
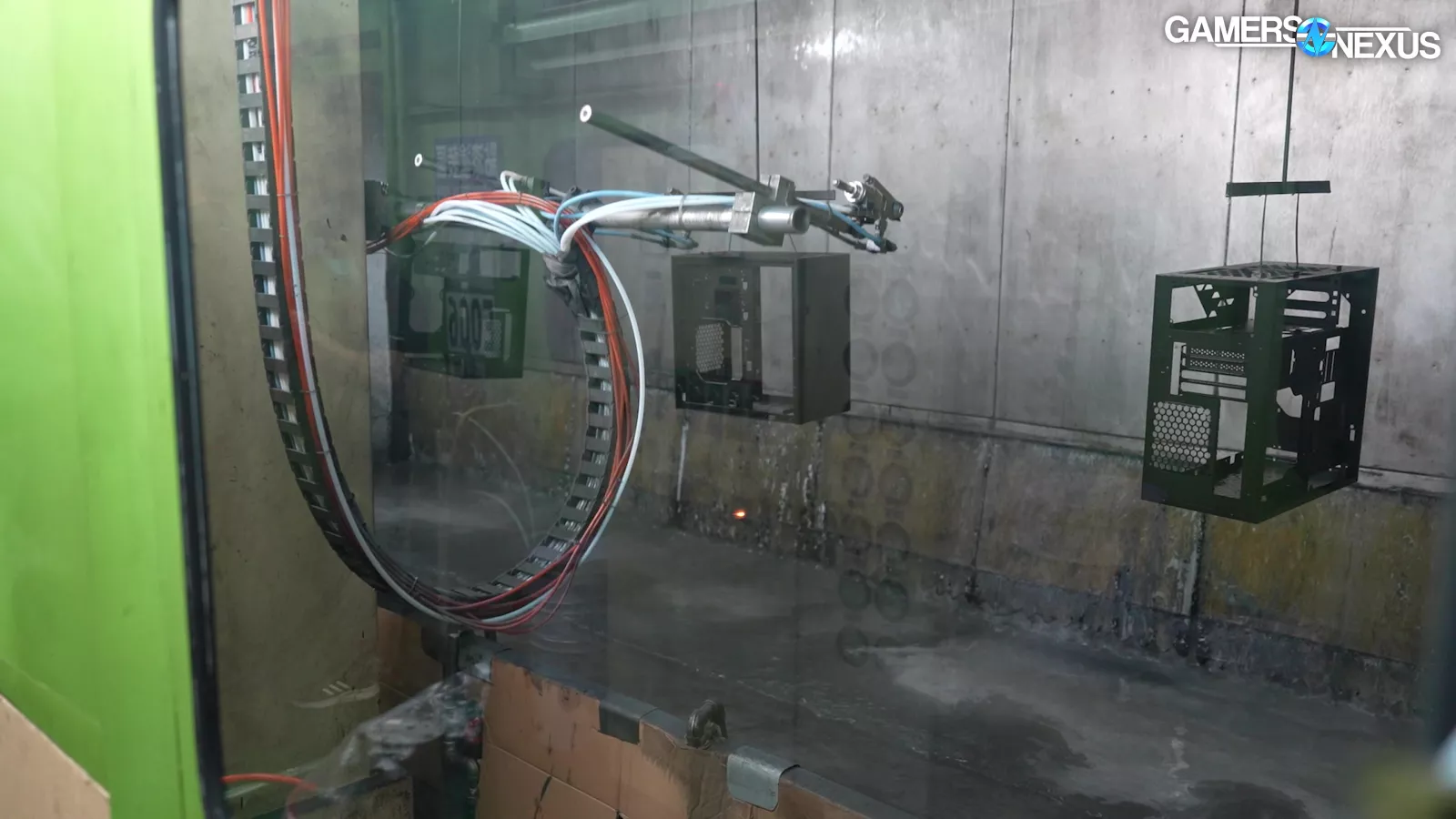
InWin is slowly modernizing all of its factories to be more like its new server facility, and many other factories in Asia have been moving increasingly to robotics -- something we’ve been showing more and more over the years. And although the grit of a machine shop and tooling factory will be blended with the sterile precision of robots, the frenetic pace of these factories will never go away.
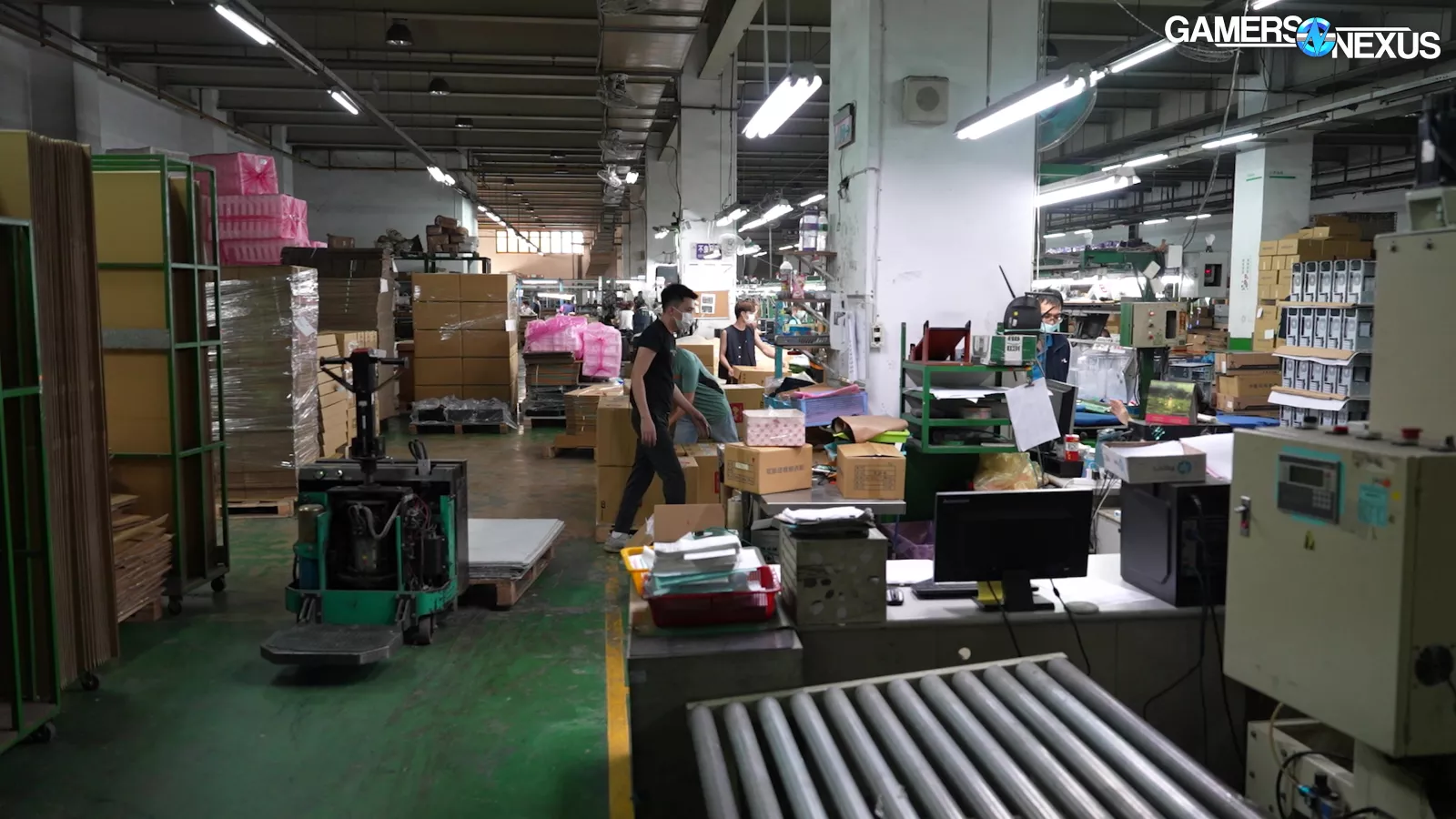
In our time at these factories, we saw constant movement and an unspoken understanding between everyone working who needed to be where and when.
To see the differences between the quiet and collaborative design rooms filled with inspirational artwork, bright colors, and art books packed with future case designs and the factories in which they’re made is a privilege of ours, and we’re excited to continue reporting on what’s really behind the products you buy in the PC industry. If you want to learn more about the front-end of product design prior to manufacturing, check out our tour of InWin’s design room.
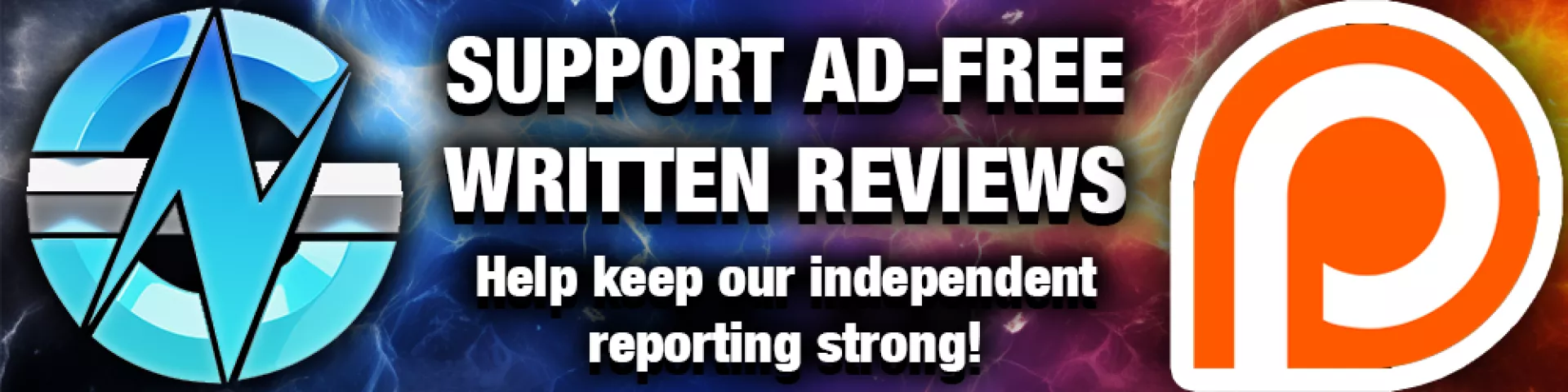
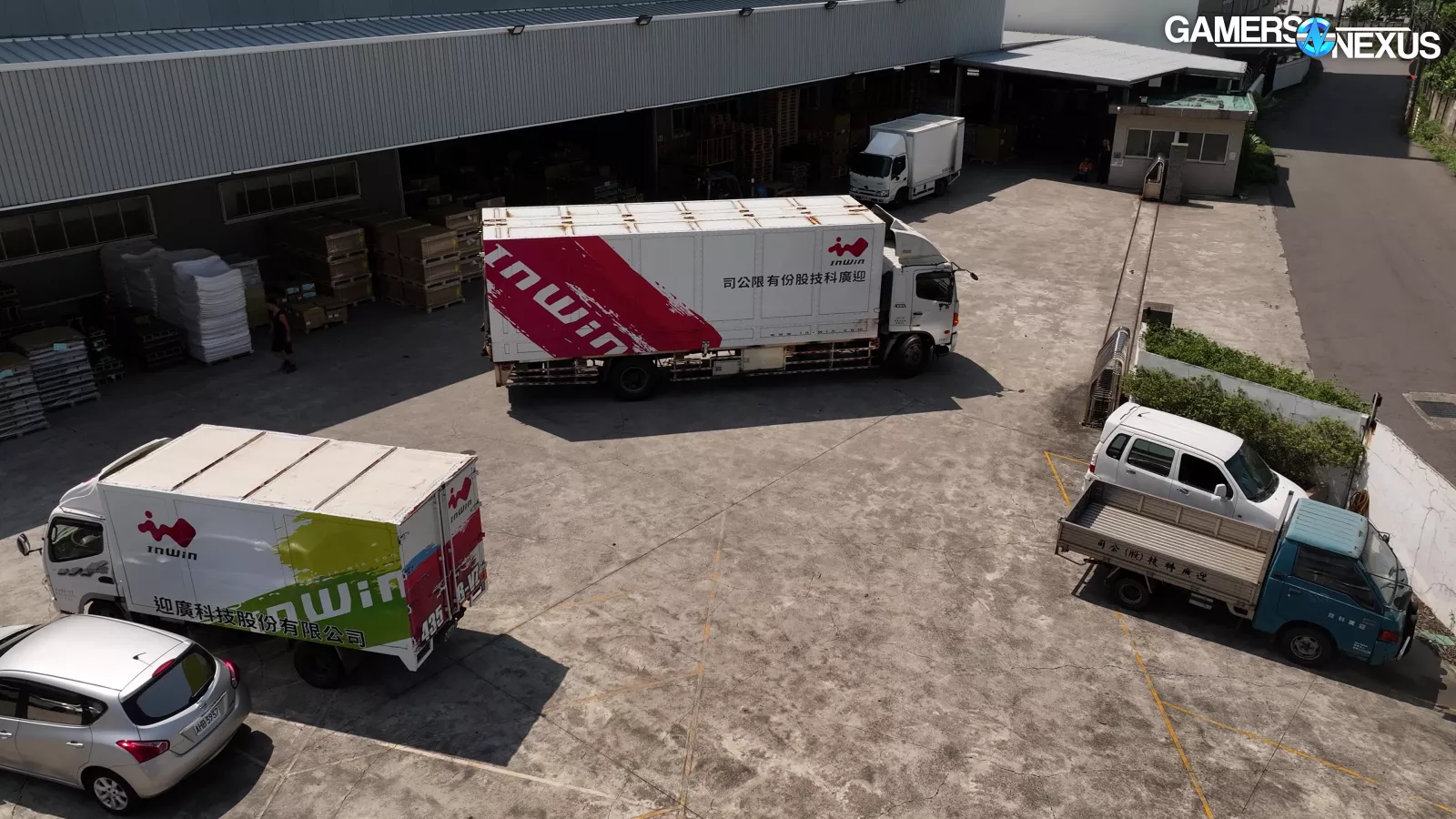
After all of these steps, the products finally get packaged outside and shipped in the millions to PC builders and data centers around the world. In our upcoming tours, we’ll be looking at RAM programming and automation, bearing manufacturing, and lasers -- so make sure to check back regularly.